Aluminum Alloy Casting Company's Process
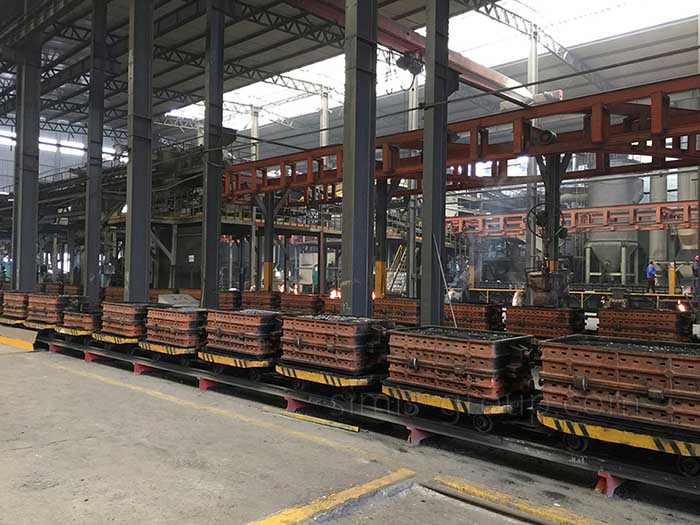
Sand Casting
Sand casting uses sand as the casting material, then pours molten aluminum into the casting mold, takes out the casting after cooling, cleans and post-processes it.
· The mold manufacturing cost is low and can be used many times
· Casts large and medium-sized aluminum castings with complex shapes and large sizes.
· Suitable for small, medium and large batch production.
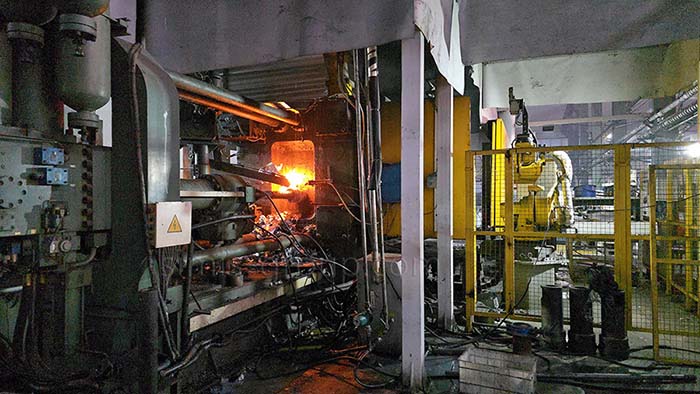
Die Casting
Die casting is a process that uses high pressure to inject molten aluminum alloy into a metal mold cavity to quickly fill the cavity and solidify. It is suitable for mass production of thin-walled, complex, and high-precision parts.
· The aluminum casting surface is smooth and the dimensional accuracy is high.
· The production cycle is short and suitable for mass production.
· The metal loss is small and the cooling in the mold is fast.
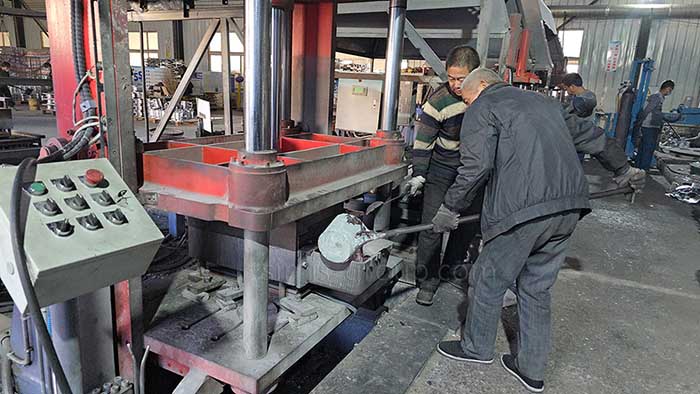
Gravity Casting
Gravity casting usually uses metal molds or sand molds, and the aluminum solution solidifies and forms under natural conditions. It is suitable for parts of medium complexity.
· The mold cost is low and suitable for small and medium batch production.
· Larger aluminum alloy parts can be produced with better density.
· The parts produced are relatively cheap.

Investment Casting
Investment casting uses soluble or combustible casting molds (such as wax molds) to make castings, and is often used to make aluminum parts with complex shapes and high precision requirements.
· High surface quality
· No need for a lot of post-processing
· Suitable for small batches and high precision parts
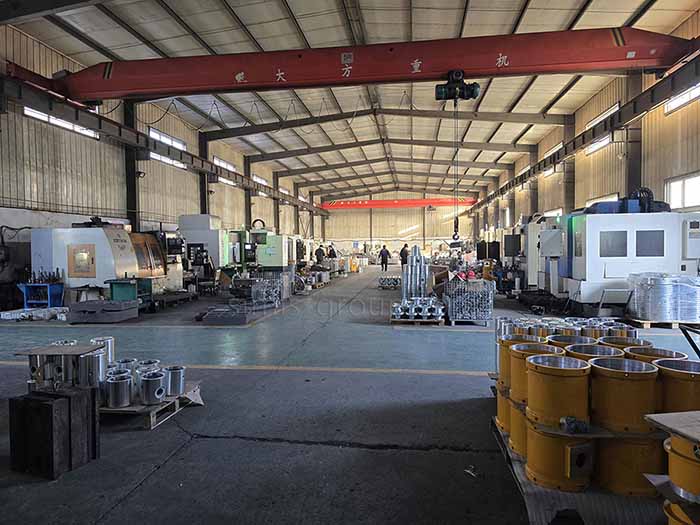
Machining
Machining is a post-processing process for aluminum castings, which improves the accuracy, surface quality and functionality of aluminum alloy castings through fine processing.
· Optimize appearance quality
· Improve aluminum part structure and function
· Process thin walls and complex shapes
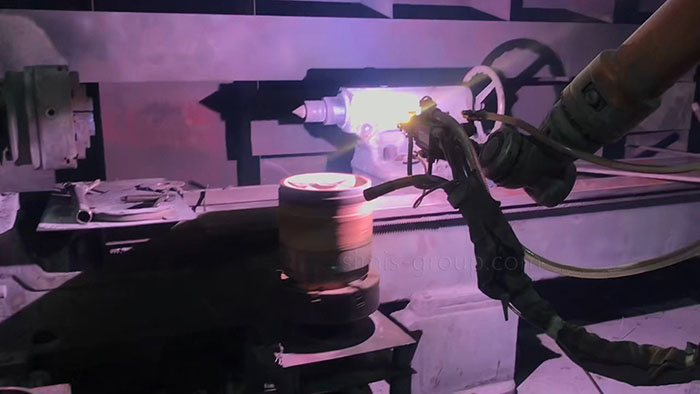
Surface Treatment
Surface treatment can transform the surface of aluminum castings by physical, chemical or mechanical means to improve the surface quality of castings, increase their durability, and improve appearance and functionality.
· Improve surface hardness
· Improve appearance and improve dimensional accuracy
· Improve adhesion and corrosion resistance
Different Materials Of Casting Aluminum Alloy

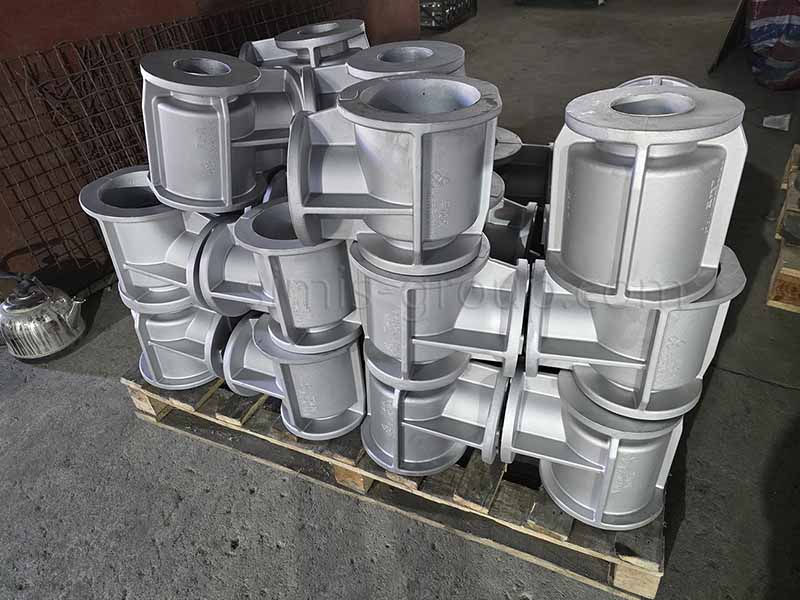
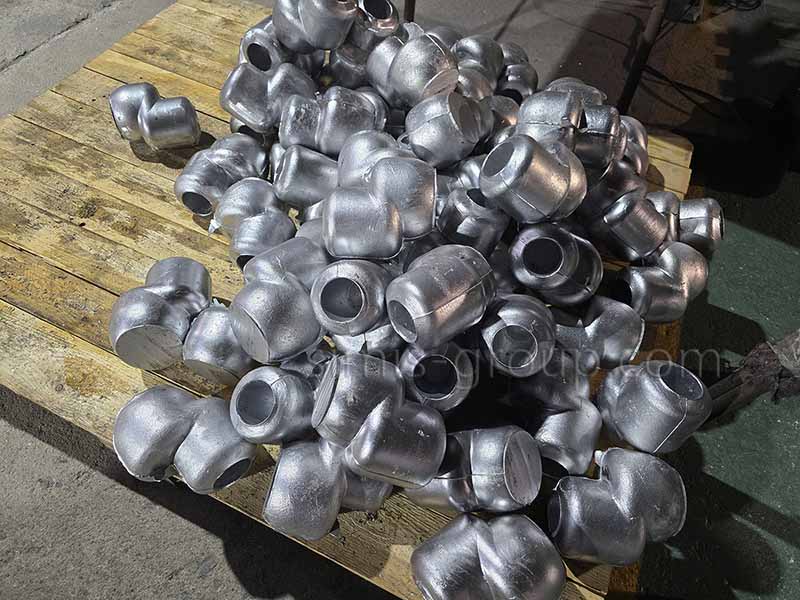
1. Aluminum-Silicon Alloy
Aluminum-silicon alloys are the most widely used materials in cast aluminum alloys, with good fluidity, corrosion resistance and wear resistance.
· Good casting performance, suitable for gravity casting and die casting processes.
· Excellent corrosion resistance and oxidation resistance.
· Good mechanical properties, some alloys can be optimized by heat treatment.
2. Aluminum-Copper Alloy
Aluminum-copper alloys are known for their high strength and high temperature resistance, and are suitable for applications requiring high loads and high temperatures.
· Higher strength and hardness.
· Higher heat resistance.
· Good fatigue resistance.
3. Aluminum-Magnesium alloy
Aluminum-magnesium alloys have excellent corrosion resistance and good processability and are suitable for the application of lightweight components.
· Excellent resistance to seawater and chemical corrosion.
· Lower strength, but good plasticity and toughness.
· Lightweight.
4. Other aluminum alloys
Simis can cast other common aluminum alloy materials, including aluminum-zinc alloy, aluminum-manganese alloy, aluminum-titanium alloy, etc., to meet the special needs of different industrial fields.
· Aluminum-zinc alloy: high strength and excellent fatigue resistance.
· Aluminum-manganese alloy: outstanding corrosion resistance.
· Aluminum-titanium alloy: high strength and light weight, good heat resistance, oxidation resistance, and excellent corrosion resistance.
· Special aluminum alloy: aluminum alloy developed for certain special needs.
1. Aluminum-Silicon Alloy
Aluminum-silicon alloys are the most widely used materials in cast aluminum alloys, with good fluidity, corrosion resistance and wear resistance.
· Good casting performance, suitable for gravity casting and die casting processes.
· Excellent corrosion resistance and oxidation resistance.
· Good mechanical properties, some alloys can be optimized by heat treatment.
2. Aluminum-Copper Alloy
Aluminum-copper alloys are known for their high strength and high temperature resistance, and are suitable for applications requiring high loads and high temperatures.
· Higher strength and hardness.
· Higher heat resistance.
· Good fatigue resistance.
3. Aluminum-Magnesium alloy
Aluminum-magnesium alloys have excellent corrosion resistance and good processability and are suitable for the application of lightweight components.
· Excellent resistance to seawater and chemical corrosion.
· Lower strength, but good plasticity and toughness.
· Lightweight.
4. Other aluminum alloys
Simis can cast other common aluminum alloy materials, including aluminum-zinc alloy, aluminum-manganese alloy, aluminum-titanium alloy, etc., to meet the special needs of different industrial fields.
· Aluminum-zinc alloy: high strength and excellent fatigue resistance.
· Aluminum-manganese alloy: outstanding corrosion resistance.
· Aluminum-titanium alloy: high strength and light weight, good heat resistance, oxidation resistance, and excellent corrosion resistance.
· Special aluminum alloy: aluminum alloy developed for certain special needs.
Application Of Casting Aluminum Alloy
Aluminum Alloy Casting Parts Custom
Aluminum Alloy Castings Company's Custom Steps
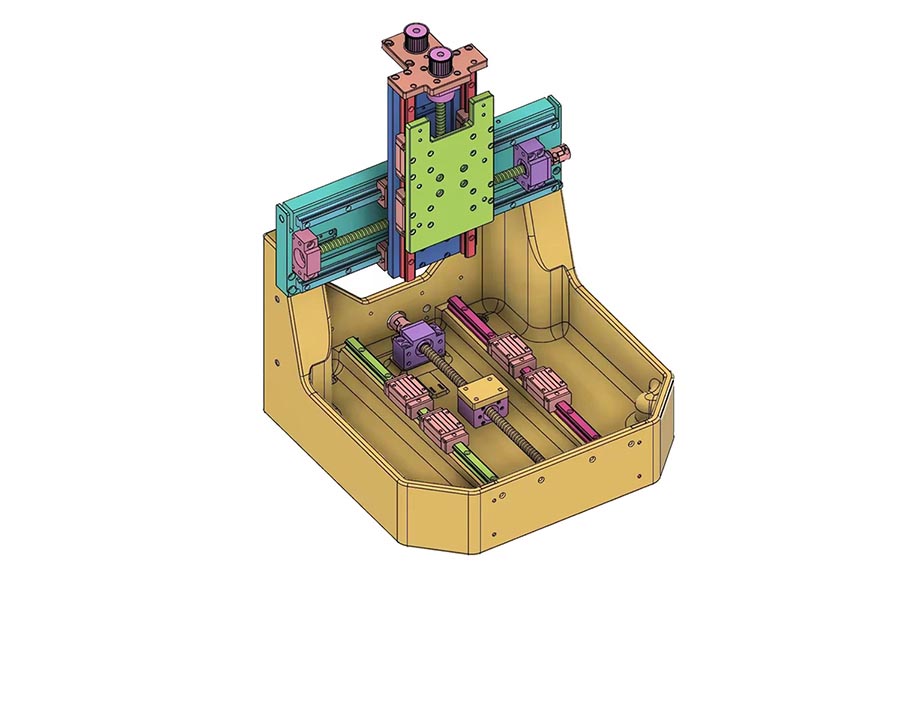
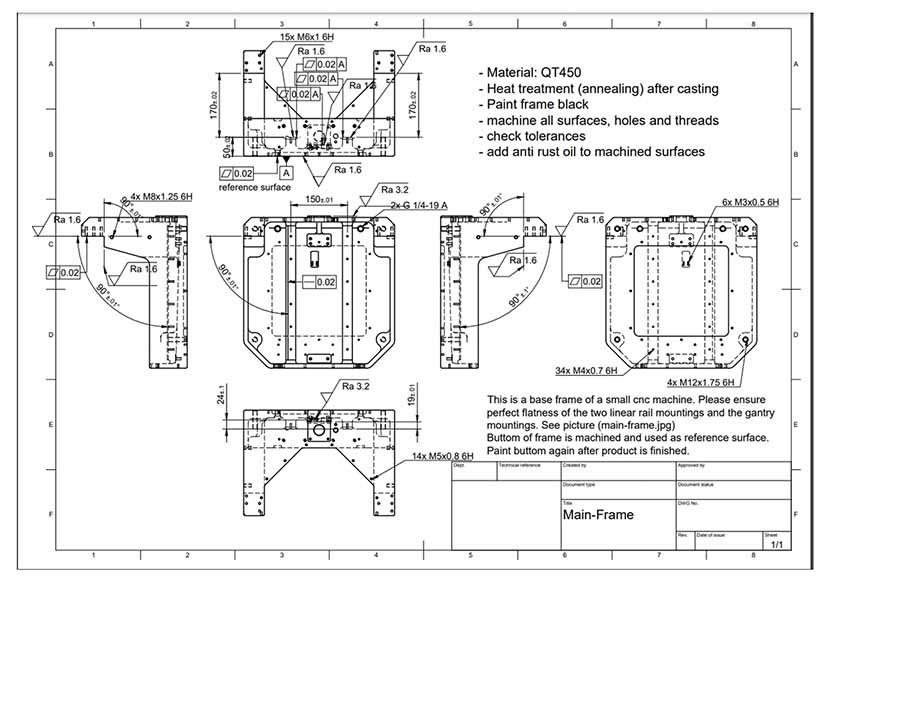

Confirm customization requirements
1. Provide detailed design documents or samples of parts
The engineering team will review the 3D drawings (CAD models) and corresponding processing plans provided by customers to ensure that they meet manufacturing requirements.
Samples: If customers provide samples, we can also produce according to samples.
2. Confirm the material of the aluminum castings
Choose the appropriate aluminum alloy material according to the use environment, technical requirements or customer requirements of the parts. We will give reasonable suggestions based on the price, mechanical properties, wear resistance, corrosion resistance, etc. of the materials.
3. Confirm the casting process
Determine the appropriate aluminum alloy casting process based on customer needs and part price, shape, size, precision, material, etc.
4. Confirm the requirements for various product attributes
Confirm the various performance requirements of the parts under the casting process and materials, such as strength, hardness, wear resistance, corrosion resistance, etc.
According to the drawings and product requirements, confirm the dimensional tolerance and precision requirements, surface roughness, appearance quality and other requirements of the product.
5. Make molds and samples
Make casting molds that meet the requirements according to the drawings or samples provided by the customer; and cast the selected casting materials through the corresponding process to produce the first batch of cast aluminum samples
6. Comprehensive inspection of samples
The produced samples will be fully inspected, including size and tolerance inspection, performance test, chemical composition analysis, non-destructive testing and other test reports.
7. Mass production
After the samples are confirmed and approved by the customer, arrange the mass production plan according to the order requirements and prepare the production materials.
Production and quality control
8. Quality control in mass production
We implement strict quality control measures during the production process to ensure that the quality of each aluminum alloy casting in mass production meets customer requirements.
Production process quality monitoring: Regular sampling during the production process to check the size, appearance, physical properties, etc. of aluminum alloy castings to ensure the consistency of each batch of parts.
Equipment inspection: Regularly inspect production equipment to avoid production deviations due to equipment failure.
9. Product quality inspection after production
Multiple inspections by multiple people: We will arrange different inspectors to conduct multiple random inspections on the final product, including dimensional accuracy, surface quality, strength, hardness, etc., to ensure that the cast aluminum parts produced meet customer requirements.
Quality inspection report: Provide a detailed quality inspection report for each aluminum alloy casting inspected.
10. Parts packaging and delivery
Packaging: For parts that pass the quality inspection, pack and ship them, choose the appropriate packaging method and the appropriate logistics method (such as air, sea, and land transportation) to avoid damage during transportation and deliver them to customers on time.
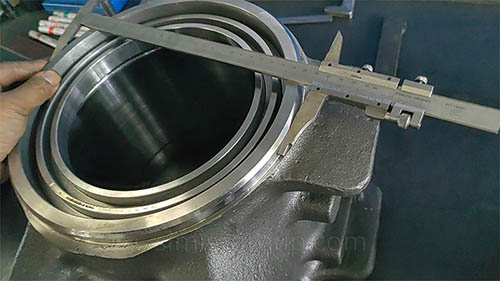
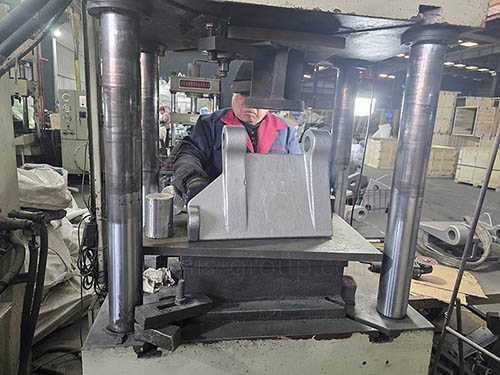
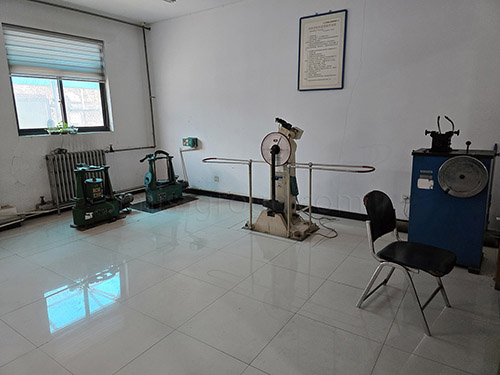
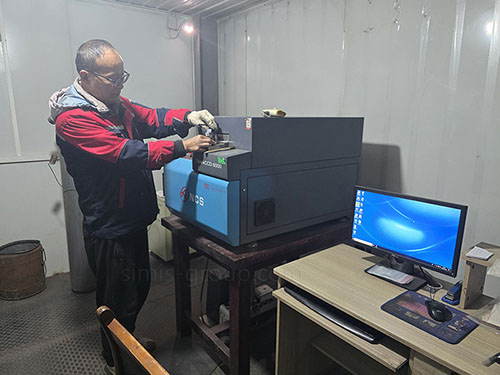
If you want to custom parts, please send me the design drawings and 3D drawings of theparts you want to customize by email, and we will calculate an accurate price for you bylooking at the detailed part parameters and 3D model.