Simis Ring Forging Factory
SIMIS Ring Forging Factory Introduction
Simis Ring Forging Factory provides a variety of precision ring forgings from small to large. It can ring forge carbon steel, alloy steel, stainless steel, titanium alloy, nickel alloy and other metal materials for aerospace, energy, automobile, machinery manufacturing, petrochemical and other industries.
In the production process of ring forging, Simis Ring Forging Factory adopts efficient heating, forging, cooling and inspection methods, especially in the production of large and high-strength ring forgings, which can achieve high-precision and high-strength forging of complex-shaped parts, ensuring the mechanical properties, dimensional accuracy and surface quality of the parts are optimized.
Ring Forging Process
Ring Forging process overview
Ring forging can process metal materials into ring parts with inner holes and outer circles. It is used in aerospace, energy, chemical, petroleum, metallurgy and other industries, especially in the production of high-strength, large-size ring parts (such as aircraft engine parts, pressure vessels, pipeline flanges, etc.).
1. Metal material preparation
Select metal alloys with good mechanical properties as raw materials. For some special materials, pretreatment such as deoxidation and impurity removal is required.
2. Billet heating
The billet is heated by equipment such as induction heating furnace to improve the plasticity of the metal and facilitate the subsequent forging process.
3. Preliminary forging (rough forging)
Free forging or die forging is performed on the heated billet to gradually transition the billet shape from the initial shape (ingot) to a ring.
4. Forging (forming process)
Ring formation: To form the final ring parts, professional ring forging dies are required. There are usually two main methods:
Closed die ring forging: The blank is gradually formed from the outer ring or inner hole through the forging die. This method can better control the dimensional accuracy of the ring parts.
Open die ring forging: The blank is made into a ring by applying uniform compression or shearing force. This method is mainly suitable for simpler ring parts.
5. Cooling process
Cooling is performed by natural air cooling or controlled cooling speed. For special alloys, the cooling speed needs to be controlled to avoid cracks or deformation caused by too fast or too slow cooling.
6. Heat treatment
Through subsequent heat treatments such as normalizing, annealing, quenching or aging, the mechanical properties of forgings are improved, internal stress is eliminated, and hardness, toughness and other properties are improved.
7. Deburring and finishing
Forged rings have burrs, which need to be removed by mechanical cutting, grinding, sandblasting and other methods.
8. Surface treatment
Through surface treatments such as electroplating, polishing, shot peening, and spraying, the surface quality of forgings is improved, and the corrosion resistance, wear resistance, and oxidation resistance are enhanced.
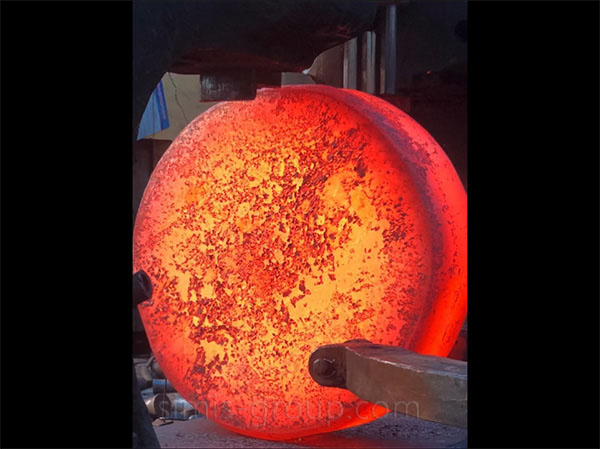
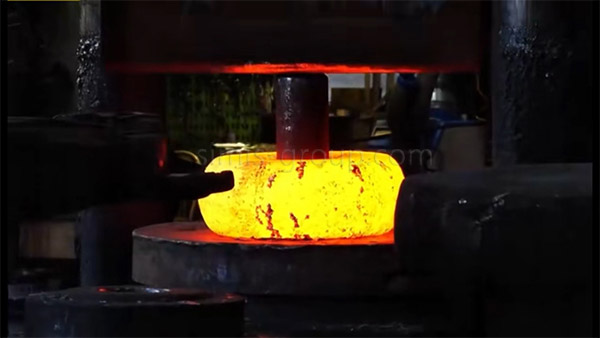
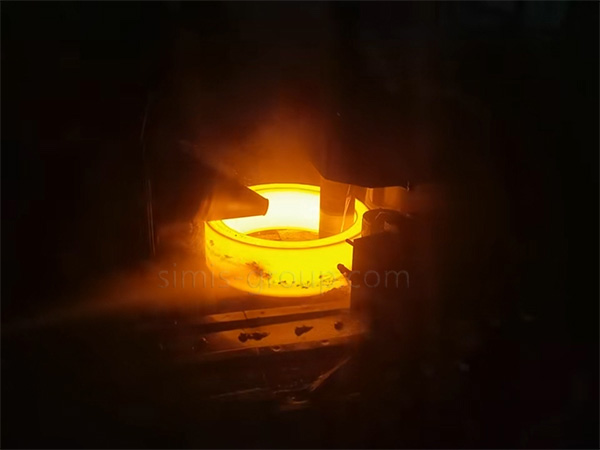
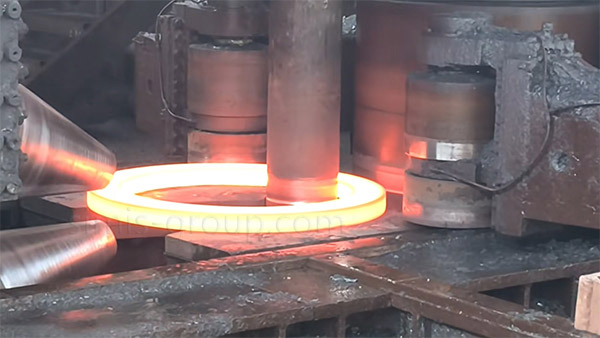
Materials Of Ring Forging
What metal parts can be forged in Simis Ring Forging Factory?
The material of ring forging is selected according to the use environment and performance requirements of the final product. Common metal materials include high-strength alloy steel (such as low alloy steel, medium carbon steel and high alloy steel), stainless steel (such as austenitic stainless steel, duplex stainless steel), titanium alloy and aluminum alloy. The material selection of ring forging process needs to consider the performance requirements of metal strength, corrosion resistance, high temperature resistance, toughness and other aspects.
1. Steel
· Carbon Steel:
Mild Steel, Medium Carbon Steel, High Carbon Steel,
· Alloy Steel:
Low alloy steel, High alloy steel,
· Stainless steel:
Austenitic stainless steel, Ferritic stainless steel, Martensitic stainless steel, Duplex stainless steel, ...
· Tool Steel:
High speed tool steel, Cold work tool steel, Hot work tool steel, ...
2. Aluminum Alloys
· Aluminum-Silicon Alloys
· Aluminum-Magnesium Alloys
· Aluminum-Zinc Alloys
· …
3. Other Metal Alloys
· Brass
· Bronze
· Nickel alloys
· Titanium alloys
· …
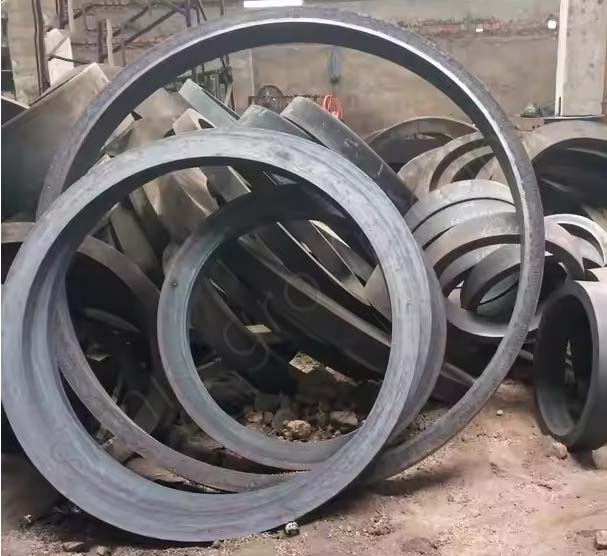
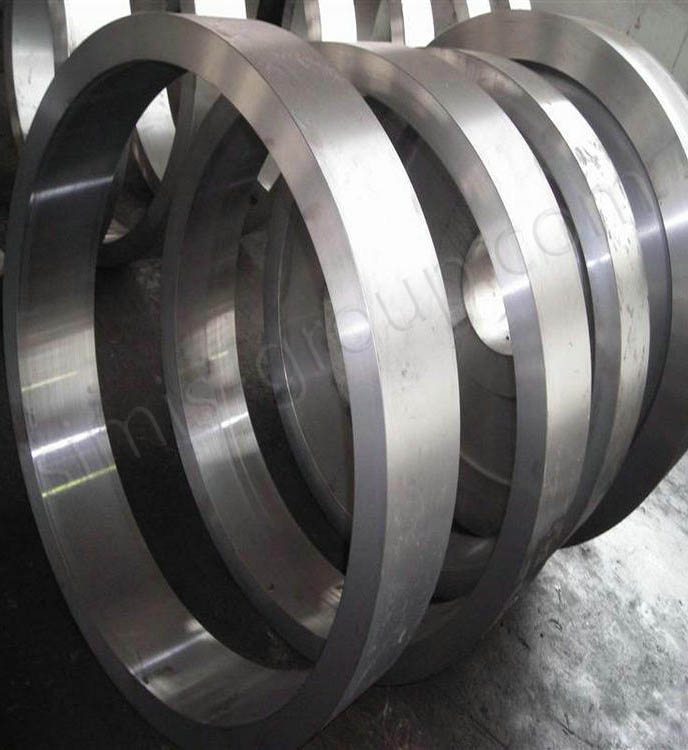
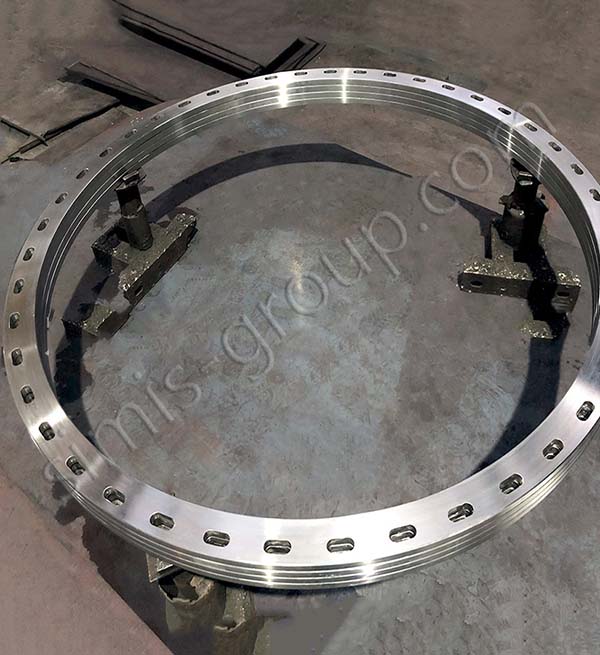
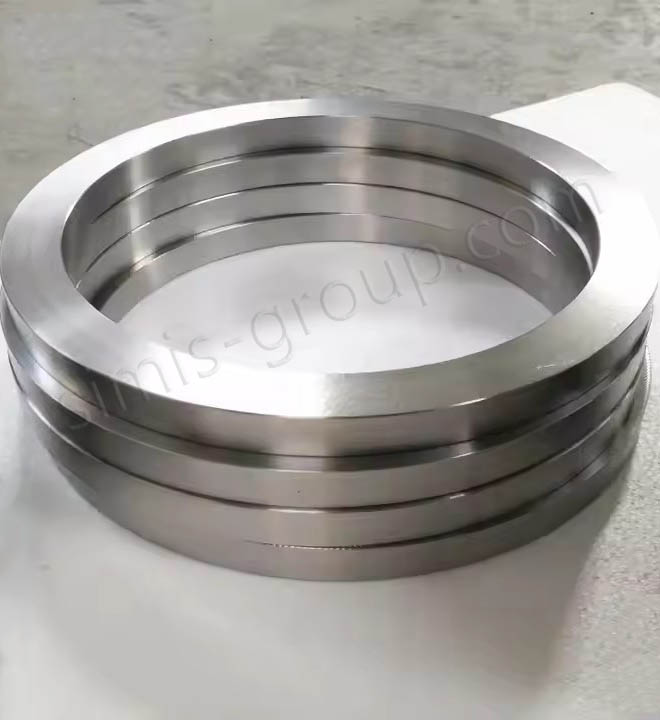