Simis Closed Die Drop Forging Factory
SIMIS Closed Die Drop Forging Factory Introduction
SIMIS Closed Die Drop Forging Factory is capable of producing forgings of various sizes and shapes, ranging from tens of grams to several tons, to meet the needs of different industries for part size and precision, including gears, shafts, flanges, hubs, bolts, etc. for automotive, aviation, energy, machinery and heavy industry.
SIMIS Closed Die Drop Forging Factory is equipped with advanced die forging equipment, including large forging hydraulic presses and forging hammers, precision mold manufacturing systems and automated production lines, which ensure the efficiency of the forging process and the consistency of forgings by using high-precision CNC technology.
Precision Closed Die Drop Forging Process
Closed Die Drop Forging process overview
Closed Die Forging (Die Drop Forging) is a process that places heated metal billets into a die with a fixed shape and then applies high pressure or forging to shape them. It can accurately produce metal parts with complex shapes and high precision. Die Forging parts are widely used in the automotive, aerospace, energy and other industries to produce important parts such as gears, shafts, flanges, gears, etc.
1. Prepare the raw materials
Select the appropriate metal blank (such as carbon steel, alloy steel, stainless steel, aluminum alloy, titanium alloy, etc.) according to the use requirements of the parts, and cut the blank to the appropriate size according to the design of the parts.
2. Heat the metal blank
Heat the metal blank to the appropriate forging temperature through a high-temperature furnace.
3. Put it into the mold and apply pressure
The heated metal blank is sent into the closed die equipment (hydraulic forging machine or mechanical forging hammer),
The forging press applies strong pressure or impact force to the die to press the metal blank into the desired shape.
4. Metal flow and forming
When pressure is applied, the metal will flow into every corner of the die and be plastically deformed to the shape of the die. The whole process may require multiple pressures or forgings until the metal completely fills the die and has the desired shape and size.
5. Cooling and solidification
After forging, the forging is removed from the die and begins to cool.
During the cooling process, the grain structure of the metal gradually solidifies, and finally forms the desired mechanical properties.
6. Heat Treatment
Depending on the material and part requirements, forgings may need to be heat treated (Annealing, Quenching, Tempering...) to improve their mechanical properties and eliminate internal stress.
7. Deburring and Post-processing
After the forgings are cooled, they may need to be machined, deburred, polished and other processes to further improve the accuracy and surface quality of the forgings.
8. Quality Inspection
Comprehensive measurement is carried out through surface quality inspection, dimension inspection, mechanical property test and other quality inspection methods to ensure that the die forgings meet the requirements of the design drawings.
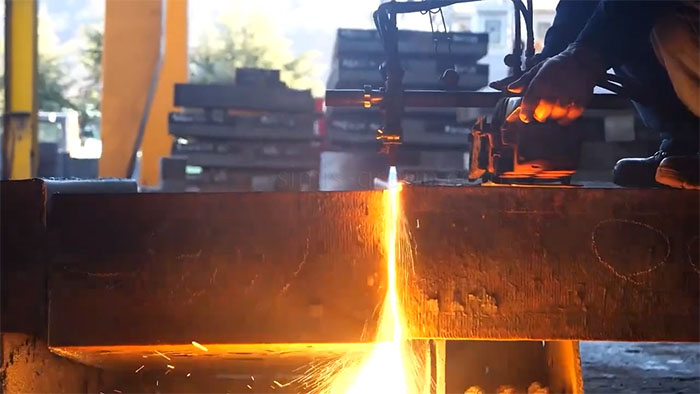
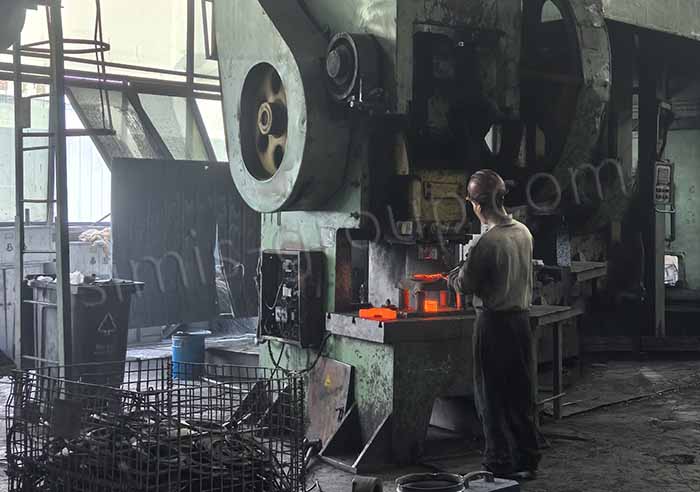
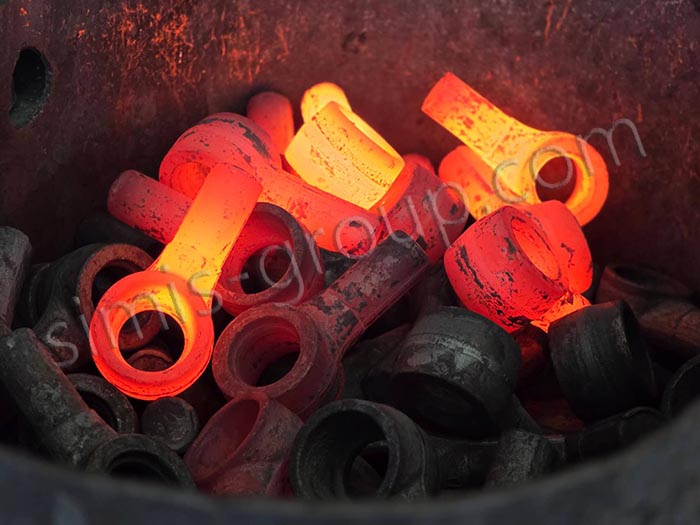
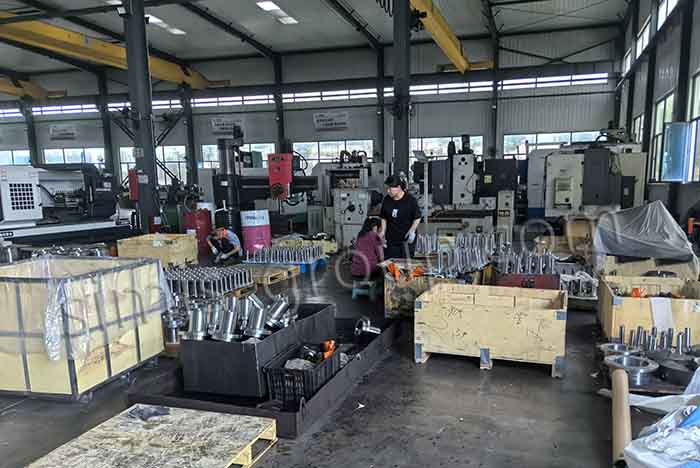
Materials of Closed Die Drop Forging
What metal parts can be forged in Simis Closed Die Drop Forging Factory?
Closed die drop forging can forge a variety of metal materials such as carbon steel, alloy steel, aluminum alloy, copper alloy, etc. These materials have different mechanical properties and corrosion resistance and are suitable for various industry applications.
Closed die forging can accurately control the forming of metal materials, so that the parts have excellent mechanical properties, surface quality and dimensional accuracy, meeting the strict requirements of aerospace, machinery, automobile, energy, chemical and other industries.
1.Steel
·Carbon Steel: Mild Steel, Medium Carbon Steel, High Carbon Steel,
·Alloy Steel: Low alloy steel, High alloy steel,
·Stainless steel: Austenitic stainless steel, Ferritic stainless steel, Martensitic stainless steel, Duplex stainless steel, ...
·Tool Steel: High speed tool steel, Cold work tool steel, Hot work tool steel, ...
2. Aluminum Alloys
·Aluminum-Silicon Alloys
·Aluminum-Magnesium Alloys
·Aluminum-Zinc Alloys
· …
3. Other Metal Alloys
·Brass
·Titanium Alloy
·Nickel Alloy
·…
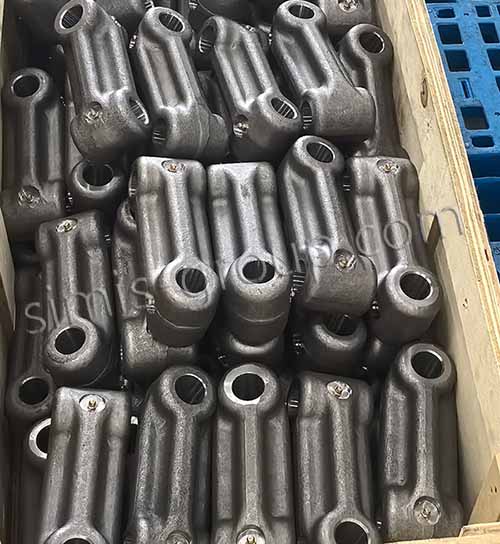
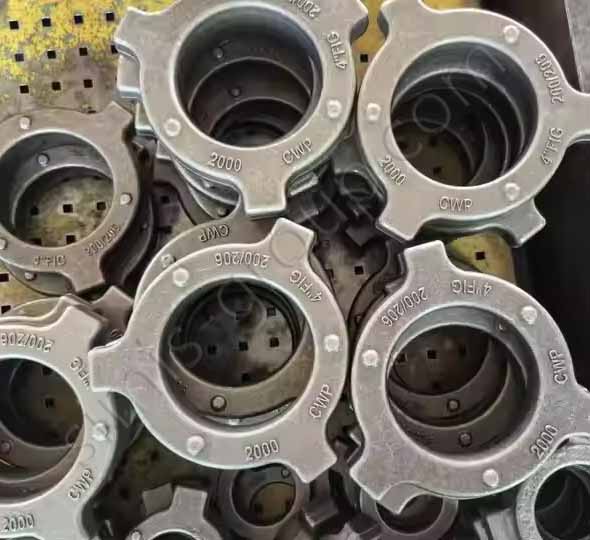
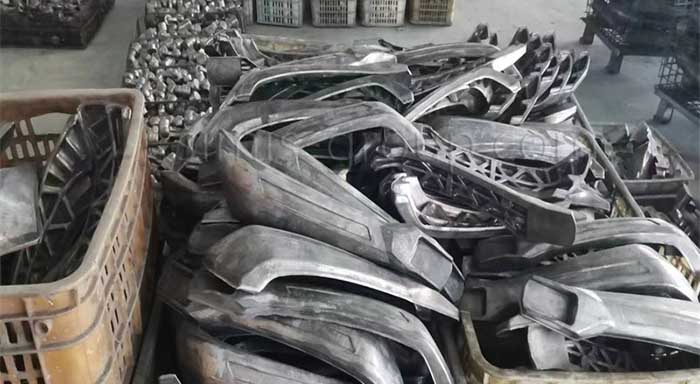
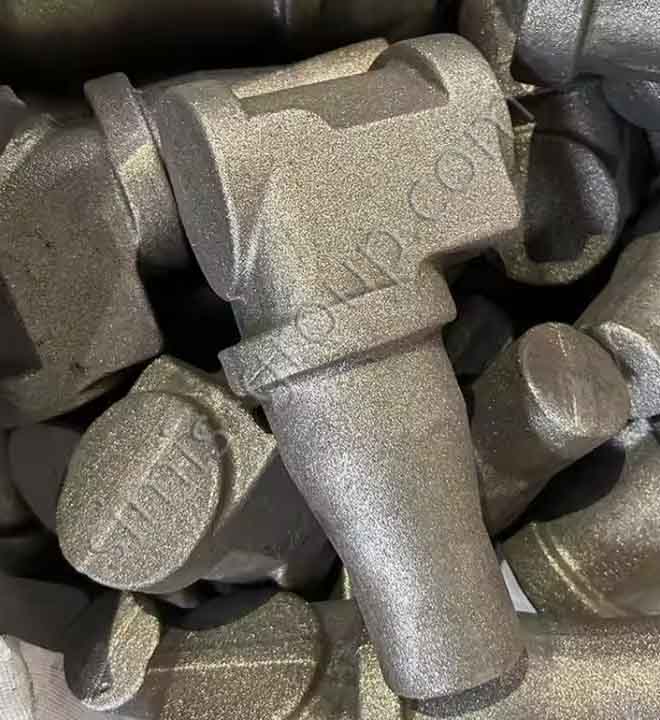