Iron Casting Company's Process
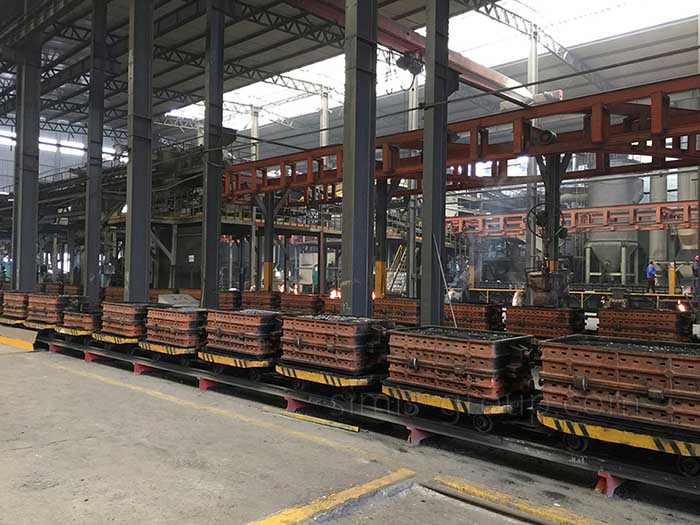
Sand Casting
Sand casting uses sand as the casting material, then pours molten iron into the mold, removes the iron casting after cooling, cleans and post-processes.
· The mold manufacturing cost is low and can be used many times
· Casts large and medium-sized cast iron castings with complex shapes and large sizes.
· Suitable for small, medium and large batch production.
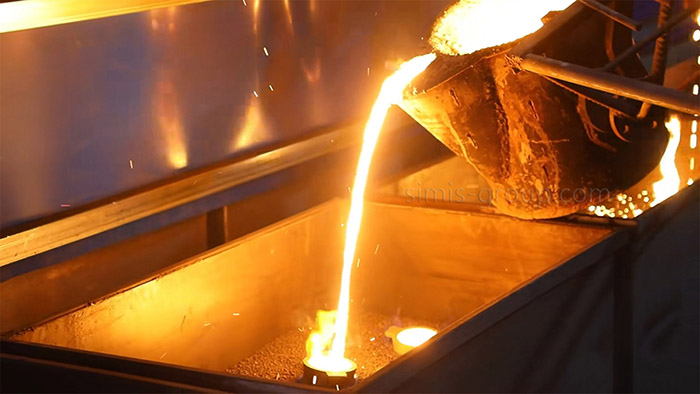
Shell Mold Casting
Shell casting uses ceramic or other refractory materials as the casting mold, and the casting mold is usually made by applying multiple layers of refractory coating on the surface of the model.
· Suitable for small batches or high-value iron castings
· Used to produce small and medium-sized iron castings
· Make complex iron castings
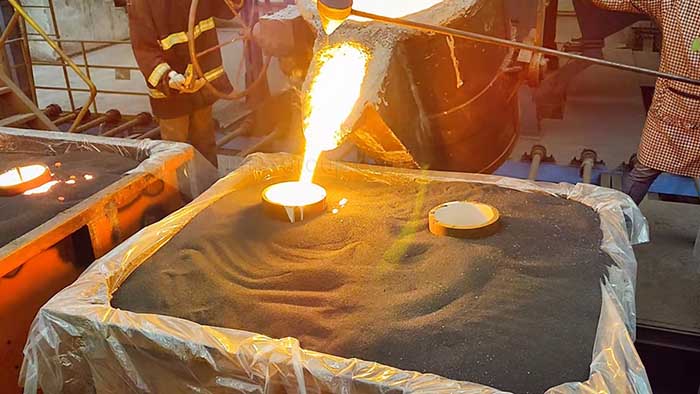
Lost Foam Casting
Lost foam casting is to form a casting mold by coating a layer of sand on a combustible model (such as foam plastic). This process does not require the removal of the foam model.
· Directly produce iron castings with complex shapes
· Lower cost and higher production efficiency
· Suitable for the production of small and medium-sized iron castings
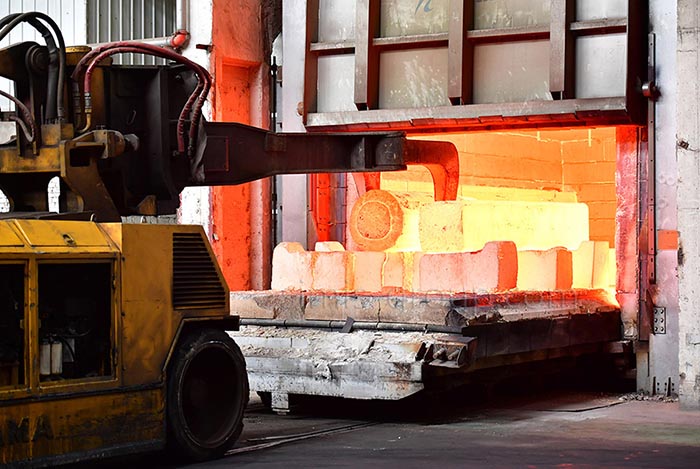
Heat Treatment
Heat treatment is to change the internal structure and properties of iron materials through heating, insulation, cooling and other processes, improve the mechanical properties of metals, extend service life, and optimize processing performance.
· Improve the hardness and strength of cast iron parts
· Improve the toughness of cast iron parts
· Improve the wear resistance and corrosion resistance of cast iron parts
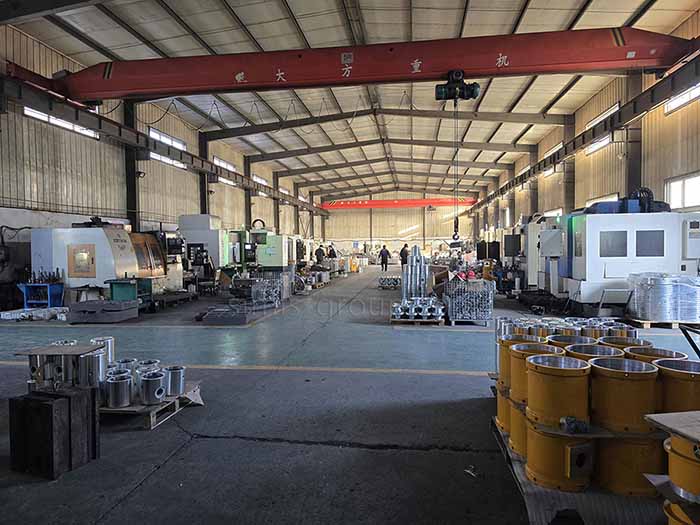
Machining
Machining is a post-processing process for cast iron parts, which improves the accuracy, surface quality and functionality of iron castings through fine machining.
· Optimize appearance quality
· Improve cast iron part structure and function
· Process thin walls and complex shapes
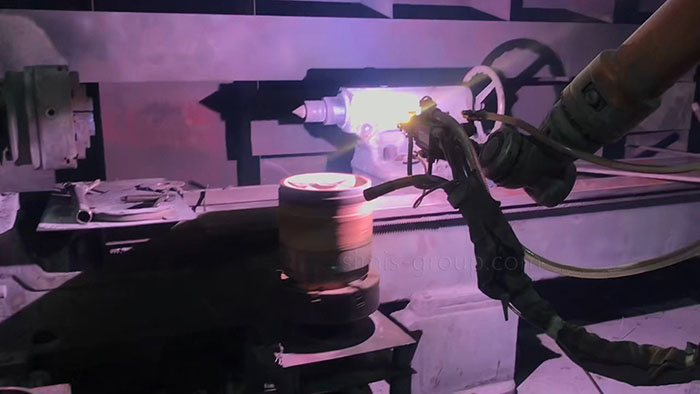
Surface Treatment
Surface treatment can change the surface of iron castings by physical, chemical or mechanical means to improve the surface quality of iron castings, increase their durability, and improve appearance and functionality.
· Improve surface hardness
· Improve appearance and improve dimensional accuracy
· Improve adhesion and corrosion resistance
Different Materials Of Cast Iron
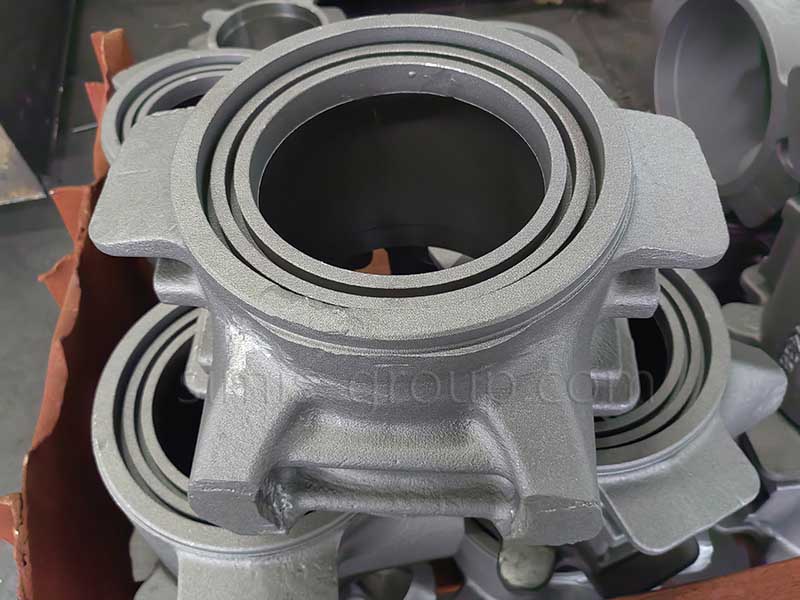
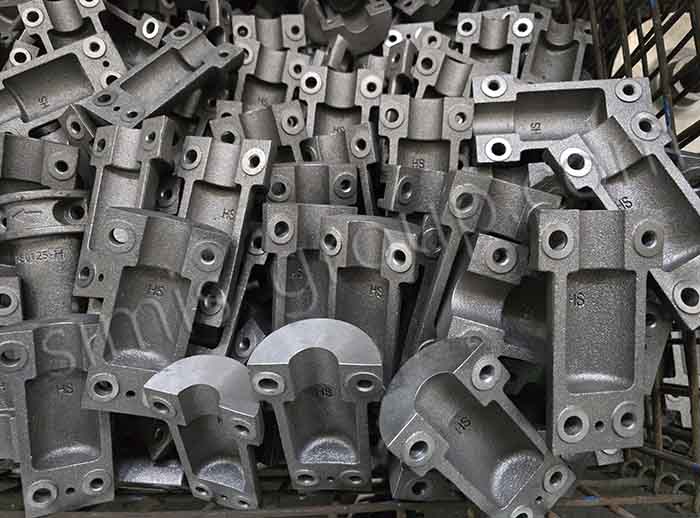
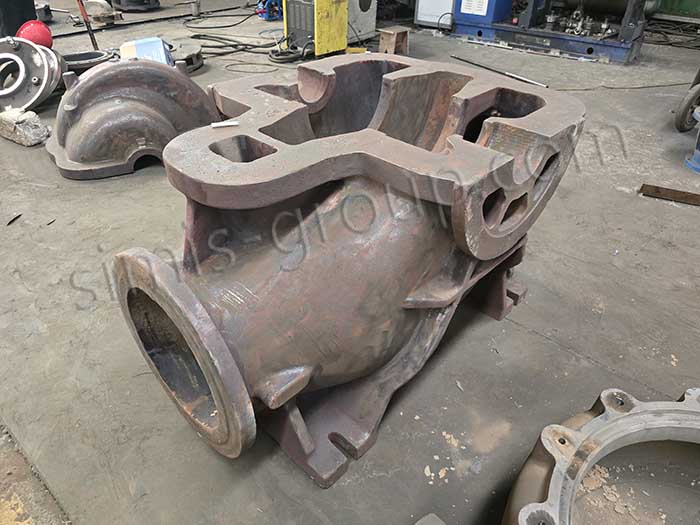
Gray (grey) iron
Gray (grey) iron has moderate strength, good castability, thermal conductivity, shock absorption and wear resistance, low cost, and is suitable for the production of castings with complex shapes and large sizes.
· Good castability: easy to cast, suitable for the production of castings with complex shapes and large sizes.
· Good shock absorption performance: the presence of graphite gives gray iron good shock absorption performance.
· Good wear resistance: suitable for manufacturing friction parts such as engine cylinders and brake discs.
· Good thermal conductivity: suitable for parts with high heat dissipation requirements.
· Good processing performance: moderate hardness, less wear on processing tools, suitable for mechanical processing.
Common gray cast iron parts: brake discs, engine cylinders, machine tool beds, pump housings, valve bodies, piping systems, etc.
Ductile Iron
Ductile iron has better strength, toughness, wear resistance and fatigue resistance than gray iron. Ductile iron parts are used in automobiles, machinery, construction, energy and other fields.
· Suitable for making load-bearing structural parts.
· Ductile iron has higher wear resistance than gray cast iron.
· Good castability, suitable for the production of complex castings.
Common ductile iron parts: automotive parts (axles, gears, engine brackets), heavy machinery parts (pump bodies, flanges, castings).
White Cast Iron
White cast iron has low carbon and silicon content, also known as chilled cast iron or cold hardened cast iron.
· It has high hardness, high brittleness, and cannot withstand impact loads.
· Very high hardness, Poor toughness, high brittleness, cannot withstand cold and hot processing
Common application parts: impeller volute, plowshare, grinding disc, furnace lining, shell lining.
Alloy Cast Iron
Alloy cast iron is also called "special performance cast iron". In the smelting process of ordinary cast iron, one or more alloying elements (common ones are nickel, chromium, molybdenum, copper, silicon, manganese, etc.) are added to adjust the composition ratio to obtain alloy cast iron with certain special properties.
· High nickel alloy cast iron.
· High chromium cast iron (Cr15, Cr20).
· Manganese cast iron
· Heat-resistant cast iron alloy: high nickel austenitic cast iron.
· Corrosion-resistant cast iron alloy: high silicon chromium cast iron, corrosion-resistant high chromium cast iron.
Gray (grey) iron
Gray (grey) iron has moderate strength, good castability, thermal conductivity, shock absorption and wear resistance, low cost, and is suitable for the production of castings with complex shapes and large sizes.
· Good castability: easy to cast, suitable for the production of castings with complex shapes and large sizes.
· Good shock absorption performance: the presence of graphite gives gray iron good shock absorption performance.
· Good wear resistance: suitable for manufacturing friction parts such as engine cylinders and brake discs.
· Good thermal conductivity: suitable for parts with high heat dissipation requirements.
· Good processing performance: moderate hardness, less wear on processing tools, suitable for mechanical processing.
Common gray cast iron parts: brake discs, engine cylinders, machine tool beds, pump housings, valve bodies, piping systems, etc.
Ductile Iron
Ductile iron has better strength, toughness, wear resistance and fatigue resistance than gray iron. Ductile iron parts are used in automobiles, machinery, construction, energy and other fields.
· Suitable for making load-bearing structural parts.
· Ductile iron has higher wear resistance than gray cast iron.
· Good castability, suitable for the production of complex castings.
Common ductile iron parts: automotive parts (axles, gears, engine brackets), heavy machinery parts (pump bodies, flanges, castings).
White Cast Iron
White cast iron has low carbon and silicon content, also known as chilled cast iron or cold hardened cast iron.
· It has high hardness, high brittleness, and cannot withstand impact loads.
· Very high hardness, Poor toughness, high brittleness, cannot withstand cold and hot processing
Common application parts: impeller volute, plowshare, grinding disc, furnace lining, shell lining.
Alloy Cast Iron
Alloy cast iron is also called "special performance cast iron". In the smelting process of ordinary cast iron, one or more alloying elements (common ones are nickel, chromium, molybdenum, copper, silicon, manganese, etc.) are added to adjust the composition ratio to obtain alloy cast iron with certain special properties.
· High nickel alloy cast iron.
· High chromium cast iron (Cr15, Cr20).
· Manganese cast iron
· Heat-resistant cast iron alloy: high nickel austenitic cast iron.
· Corrosion-resistant cast iron alloy: high silicon chromium cast iron, corrosion-resistant high chromium cast iron.
Application Of Iron Castings
Iron Casting Parts Custom
Iron Castings Company's Custom Steps
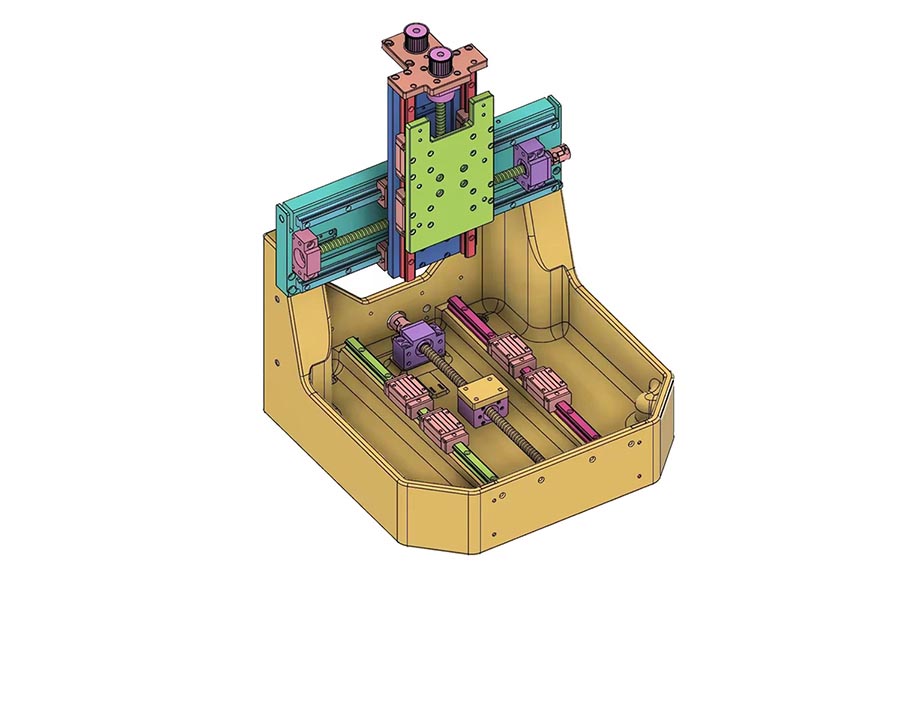
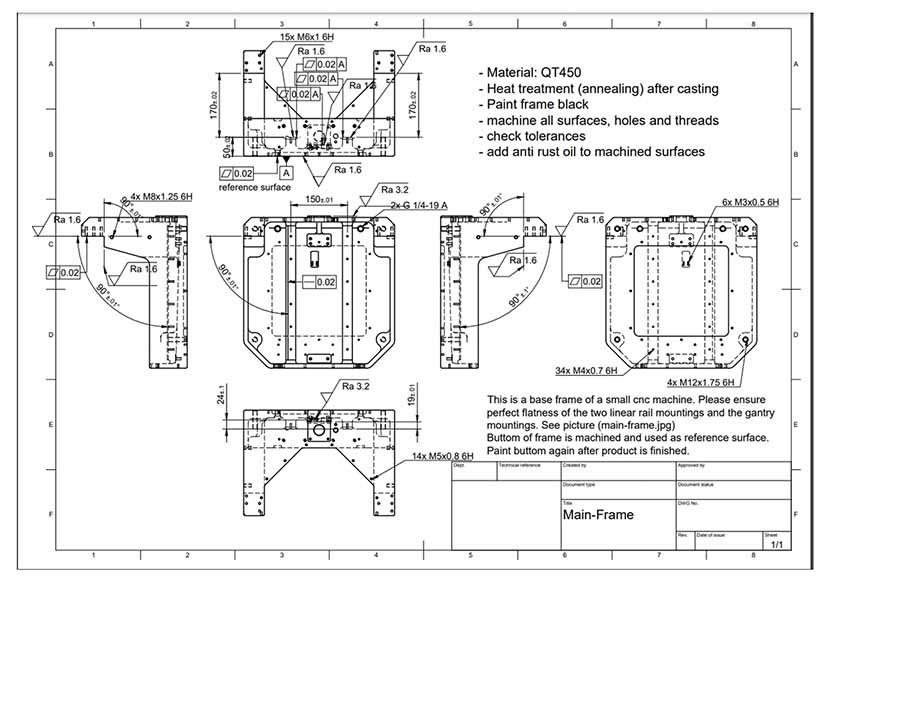
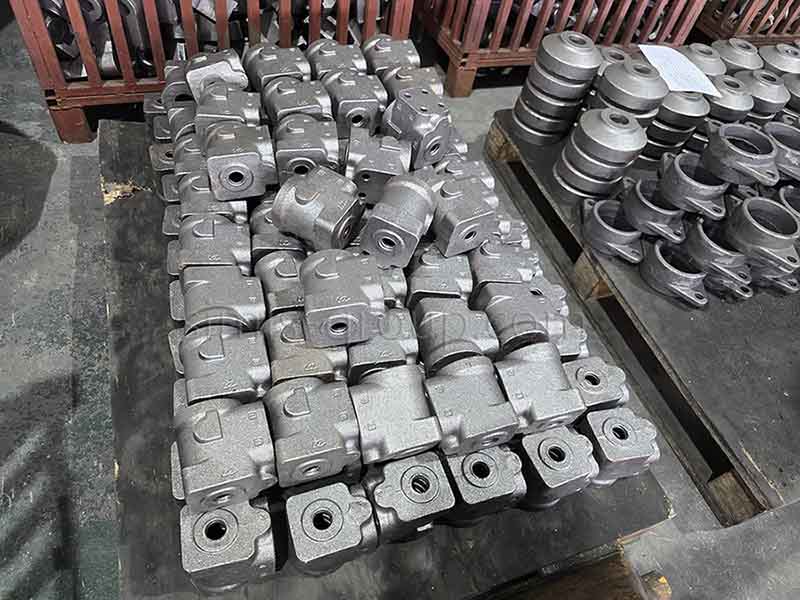
Confirm the customization requirements of cast iron parts
1. Provide detailed design documents or samples of cast iron parts
Simis engineers will analyze the 3D drawings (CAD models) and corresponding plane drawings of the parts provided by the customer to ensure that the design drawings meet the manufacturing requirements.
Whether to provide samples: If the customer can provide samples, we will produce according to the samples.
2. Confirm the requirements of various product attributes
Understand the various performance requirements of the parts, such as strength, hardness, wear resistance, corrosion resistance, etc., as well as the size, tolerance, and accuracy of the parts, and confirm the requirements of surface roughness, appearance quality, etc.
3. Confirm the material of the casting
According to the use environment, technical requirements or customer requirements of the parts, select the appropriate cast iron material. Our engineers will give suggestions based on the price, mechanical properties, wear resistance, corrosion resistance, etc. of the material.
4. Confirm the casting process of the parts
According to customer needs, combined with the requirements of part price, shape, dimensional accuracy, material, etc., determine the casting process suitable for part production.
5. Make molds and samples
According to the drawings or samples provided by the customer, make casting molds that meet the requirements, and cast the selected cast iron material through the corresponding process to produce the first batch of samples.
6. Comprehensive inspection of samples
The samples produced will be fully inspected to ensure that they meet the design standards and customer quality requirements,
and test reports such as size and tolerance inspection, performance testing, chemical composition analysis, and non-destructive testing.
Production and quality control
7. Mass production
After the sample is confirmed and approved by the customer, the mass production plan is arranged according to the order requirements and the production materials are prepared.
The same casting equipment and process as the sample stage are used in the mass production process to ensure the consistency of each batch of cast iron castings.
8. Quality control in mass production
We implement strict quality control measures during the production process: regular sampling during the production process to check the size, appearance, physical properties, etc. of cast iron parts to ensure the consistency of each batch of parts and meet customer requirements.
9. Product quality inspection after production
Multiple inspections by multiple people: We will arrange different inspectors to conduct multiple sampling inspections on the final product, including dimensional accuracy, surface quality, strength, hardness, etc., to ensure that the produced cast iron parts meet customer requirements.
10. Parts packaging and delivery
Packaging: Pack and ship the parts that have passed the quality inspection, choose the appropriate packaging method and the appropriate logistics method (such as air, sea, and land transportation) to avoid damage during transportation and deliver them to customers on time.
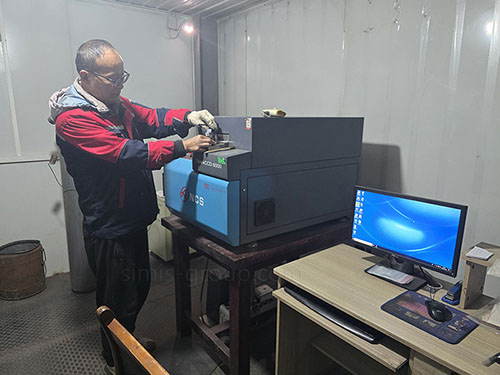
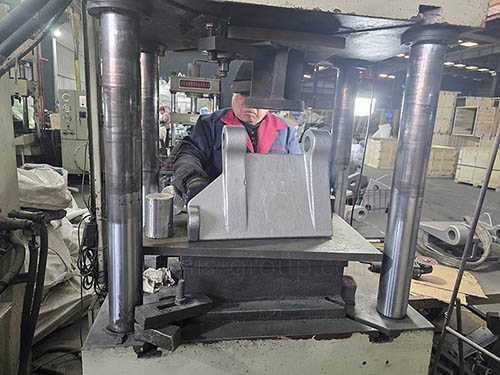
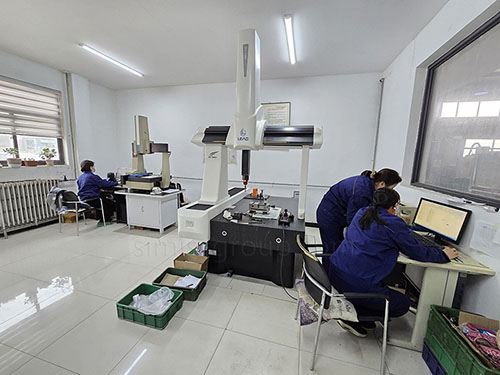
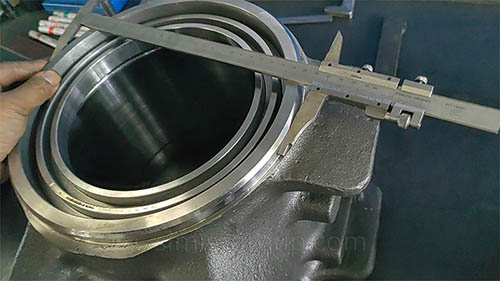
If you want to custom parts, please send me the design drawings and 3D drawings of theparts you want to customize by email, and we will calculate an accurate price for you bylooking at the detailed part parameters and 3D model.