Custom Metal Parts For Mining Metallurgical
Customized castings and forgings in the mining and metallurgical industry can be used in mining, transportation, crushing, grinding, smelting, structural support, lifting, environmental protection and energy recovery process equipment. The high strength, wear resistance and fatigue resistance provided by castings and forgings enable customized parts to operate stably under high load, high impact, high temperature and corrosive environments, which not only improves the reliability and service life of mining equipment and reduces maintenance costs, but also enables efficient, safe and green production for the mining and metallurgical industry.
Mining Metallurgical Parts Classification
1. Mining equipment components
Mining equipment is the frontier of mining production. Castings and forgings are used to manufacture key components such as bucket teeth, buckets, drill rods and rotating shafts in excavators, drilling rigs and other equipment. With excellent strength, toughness and wear resistance, they ensure that the equipment can operate stably and efficiently under complex geological conditions and high-impact environments.
· Castings: excavator bucket teeth, bucket housings, drill rig bases and supports
· Forgings: digging arm pins, rotating shafts, drill rod joints
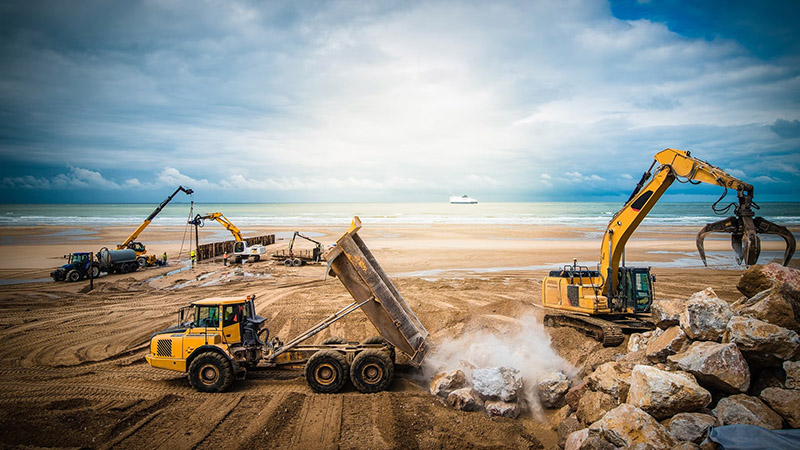
2. Conveying system components
The conveying system is the hub for the flow of ore and raw materials. Castings and forgings are widely used in rollers, sprockets, racks, drive shafts and chains. Its high rigidity and wear resistance ensure the long-term continuous operation of the conveying equipment and reduce the frequency of downtime and maintenance.
· Castings: conveyor rollers, frames, sprocket housings
· Forgings: chain segments, drive shafts and couplings
3. Crushing and grinding equipment components
Crushing and grinding equipment is an important part of ore processing. Castings and forgings are used in this field to manufacture components such as crusher housings, hammers, mill liners and spindles. Its high strength and wear resistance enable the equipment to withstand the impact and long-term wear of ore, ensuring the stability and efficiency of ore processing.
· Castings: crusher housing, mill liner, bushing
· Forgings: crusher hammer, mill bearing, spindle
4. Smelting equipment components
Smelting equipment needs to operate in high temperature, high pressure and highly corrosive environments. Castings and forgings are used for furnace housings, support rods, valves and slides, providing excellent high temperature resistance, corrosion resistance and high strength performance, ensuring stable operation of smelting equipment, extending equipment life and achieving high temperature metal smelting.
· Castings: furnace shell, air duct components, cast steel slideway
· Forgings: furnace support rods, forged valve components
5. Structural and support components
The structural stability of large-scale mining machinery and metallurgical equipment cannot be separated from the support of castings and forgings, such as racks, bases, sliding guides, bolts and support shafts. These components provide the necessary rigidity and load-bearing capacity for the equipment, enabling it to maintain stable operation under heavy load conditions.
· Castings: large racks, support bases, sliding guides
· Forgings: high-strength bolts, connectors, heavy-duty support shafts
6. Lifting and hoisting equipment components
Lifting and hoisting equipment is a key system for underground transportation and metallurgical equipment maintenance in mines. Castings and forgings play an important role in components such as drums, winches, hooks, pulleys and chain links. Its high strength and fatigue resistance ensure that the equipment maintains stability and safety during continuous high-load operation.
· Castings: winch wheels, drum housings, hooks, pulley brackets
· Forgings: wire rope chucks, lifting rings, forged spindles, chain links
7. Environmental protection and energy recovery system components
Environmental protection and energy recovery systems are important links in the green development of the mining and metallurgical industry. Castings and forgings are used for desulfurization tower shells, heat exchangers, fan blades, energy recovery rotors and other components. Their corrosion resistance, high temperature resistance, and high strength properties improve the efficiency and stability of environmental protection equipment and reduce energy consumption and environmental impact.
· Castings: flue gas desulfurization tower shell, exhaust pipe, waste heat boiler shell, heat exchanger shell
· Forgings: high-pressure fan blade shaft, energy-saving valve body, energy recovery rotor
Available Materials For Mining Metallurgical Parts
Iron
Steel
Aluminum Alloy
Other Metal Alloys
Iron
Steel
Aluminum Alloy
Other Metal Alloys
How To Customize Mining Metallurgical Parts
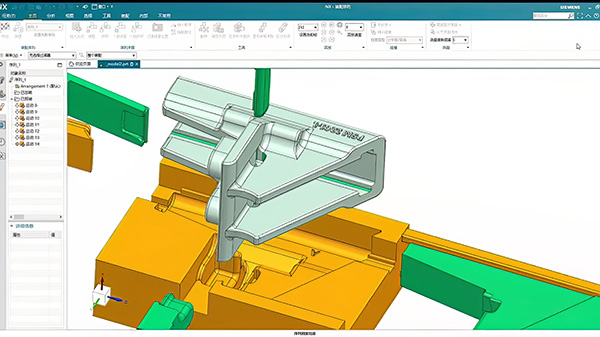
3D Drawings
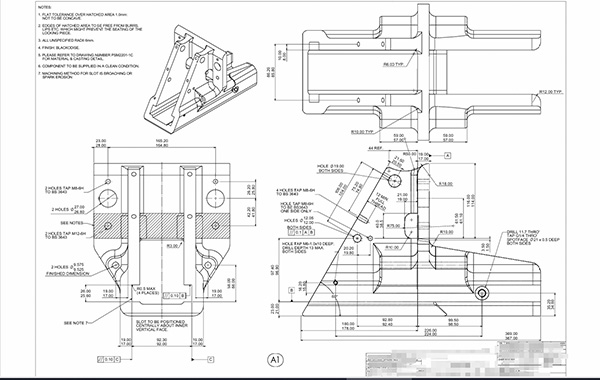
Processing Drawing
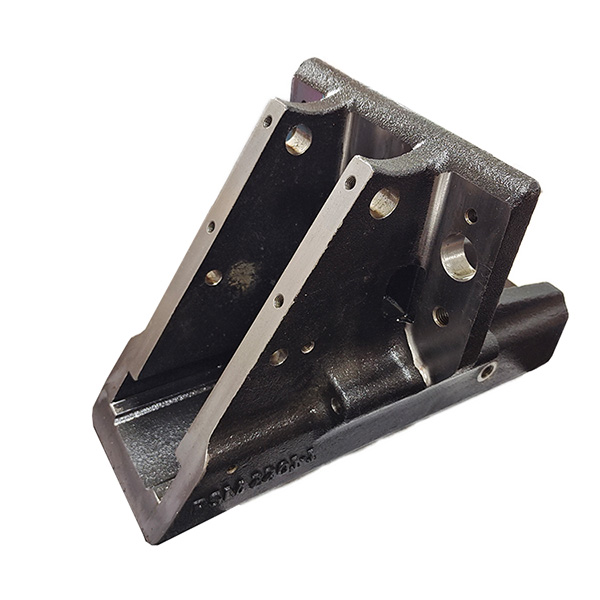
Sample
1. Provide Detailed Design Documents Or Samples
2. Confirm Material/Process/Performance
3. Make Production Molds And Samples
4. Comprehensive Sample Inspection
5. Mass Production
6. Post-production Parts Multiple Quality Inspections
1. Provide Detailed Design Documents Or Samples
2. Confirm Material/Process/Performance
3. Make Production Molds And Samples
4. Comprehensive Sample Inspection
5. Mass Production
6. Post-production Parts Multiple Quality Inspections
Custom Processing of Mining Metallurgical Parts
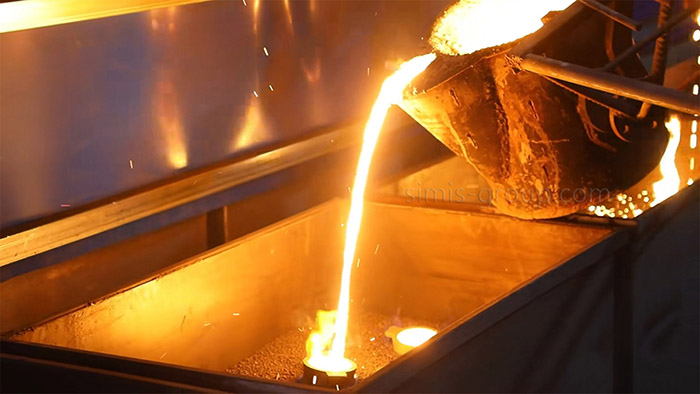
Casting
In the mining and metallurgical industry, the casting process can efficiently produce parts with complex shapes and large sizes, such as crusher housings, furnace components and other mining machinery components. It is especially suitable for manufacturing structural parts that meet the specific performance requirements of the mining and metallurgical industry.

Forging
Forging is a process that uses compression to shape metal, increasing the material's strength and toughness. Forging is used in the mining and metallurgical industries to produce durable parts such as shafts, gears and heavy equipment components that must withstand extreme pressure and wear in equipment such as crushers, mills and excavators.
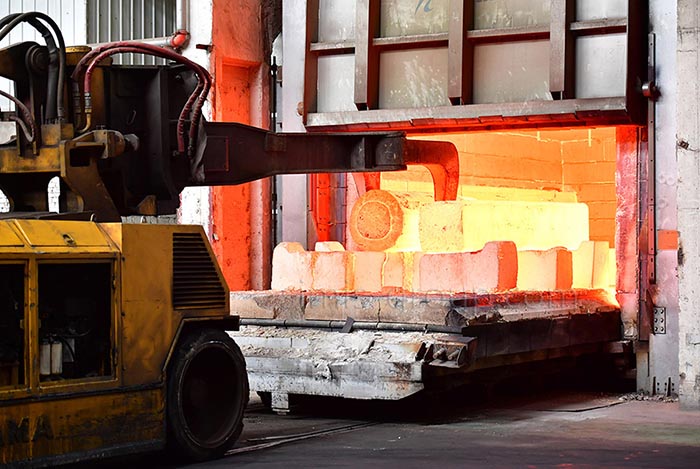
Heat Treatment
Heat treatment is a process that heats and cools metals to change their mechanical properties. In the mining and metallurgical industries, it is often used to increase the hardness, wear resistance and fatigue strength of key components such as crusher jaws and mill liners, thereby improving their durability in harsh environments.

Machining
Machining is the process of removing material from a workpiece using cutting tools to achieve precise shapes and dimensions. In the mining and metallurgy sectors, machining is used to manufacture high-precision parts such as pump components, conveyor rollers, and specialized tools that require exact tolerances to function properly and efficiently.
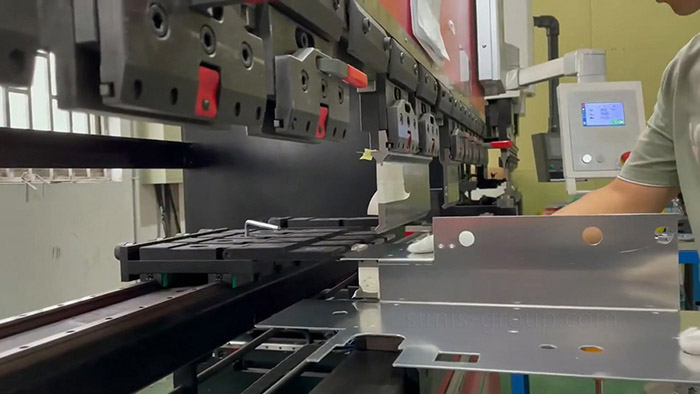
Sheet Metal Fabrication
Sheet metal fabrication is the process of cutting, bending and welding sheet metal to form structural components. In the mining and metallurgical industries, sheet metal fabrication is used to create components such as equipment housings, protective covers and structural frames that are lightweight yet durable and provide protection and integrity under harsh operating conditions.
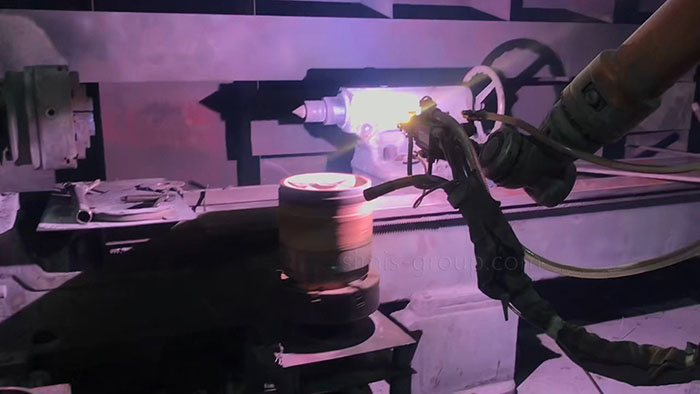
Surface Treatment
Surface treatment includes processes such as coating, electroplating, anodizing, etc. to enhance the surface properties of materials and improve corrosion resistance and wear resistance. In the mining and metallurgical fields, surface treatment processes are used for components such as crusher liners and grinding media to extend their service life and reduce maintenance, ensuring reliable performance in abrasive environments.