Steel Forging Company's Process

Open-die Forging
Open free forging is to deform the metal after heating it through the direct action of a forging hammer or press, gradually forming it into the desired shape and size.
· High flexibility, no mold required, and can process steel forgings of various shapes
· Can manufacture large, high-strength steel forgings
· Low manufacturing cost, suitable for single-piece and small-batch production.
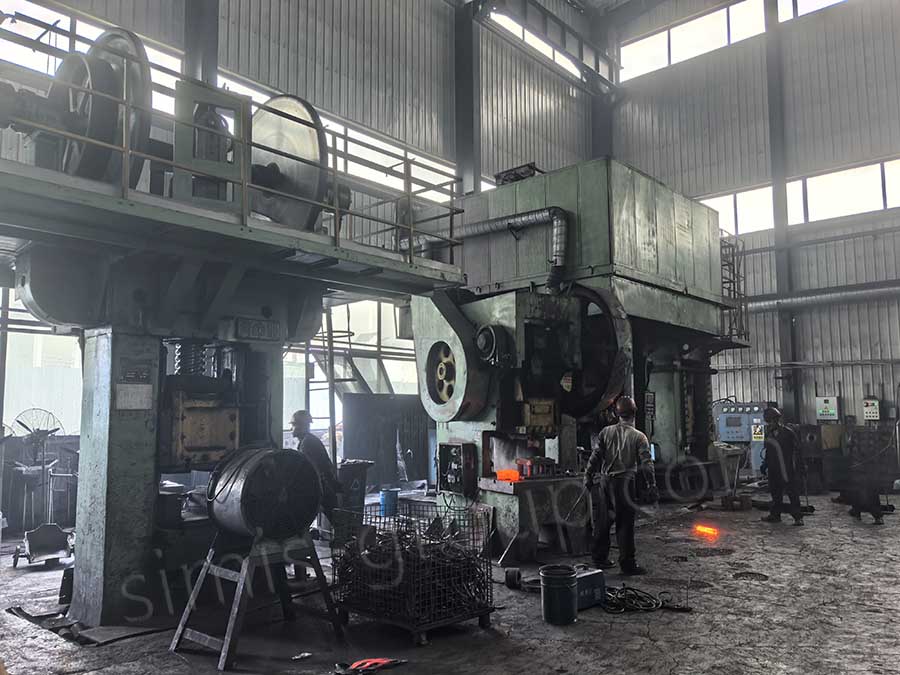
Closed Die Drop Forging
Closed die forging is to heat the metal material to a certain temperature and then forge it through a special closed die. It can produce steel forgings with high precision, excellent mechanical properties and good surface quality.
· Suitable for mass production
· High dimensional accuracy of steel forgings
· Excellent mechanical properties of steel forgings
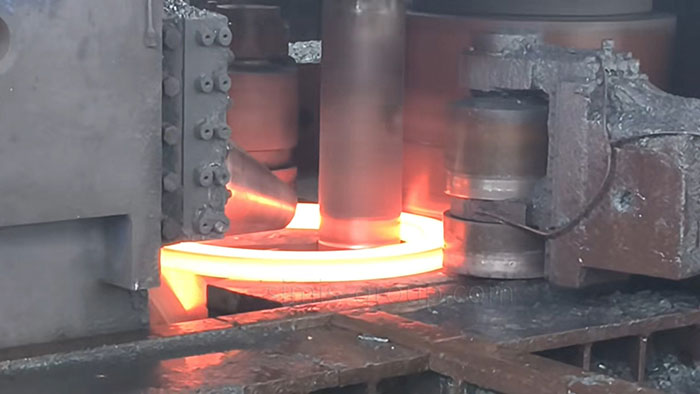
Ring Forging
Ring forging is specially used to produce ring parts. After heating the steel blank, it is placed in a mold or forging equipment, and pressure is applied to force the metal to flow into the mold cavity to form a steel ring forging.
· Used to make parts with complex shapes
· Suitable for medium and large-scale production
· Forgings have high strength and toughness
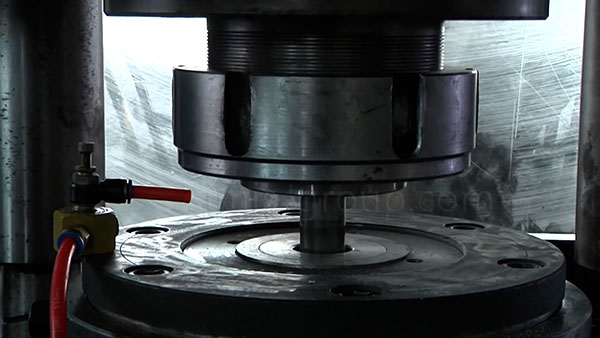
Cold Forging
Cold forging is the process of plastically deforming a steel blank by applying pressure at room temperature without heating, thereby achieving high precision and improved mechanical properties.
· Tight tolerances and good surface finish
· Increased strength and hardness of the steel, improving durability
· Reduced material waste and the need for secondary processing
· Steel forgings have higher strength and toughness
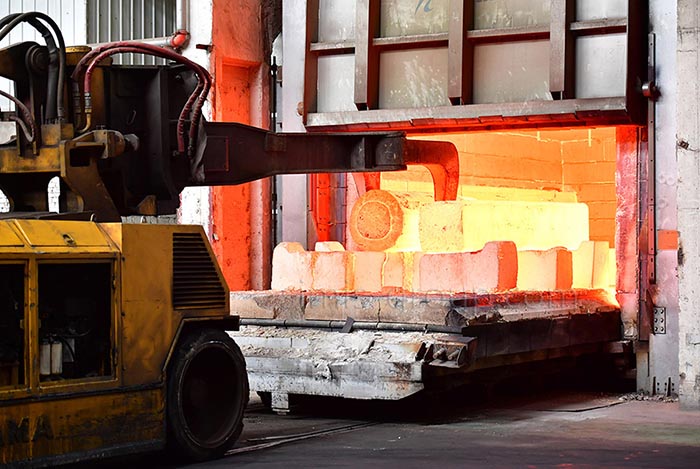
Heat Treatment
Heat treatment is to change the internal structure and properties of steel materials by heating, heat preservation and cooling, improve the mechanical properties of steel, extend service life and optimize processing performance.
· Improve the hardness and strength of steel materials
· Improve the toughness of steel materials
· Improve wear resistance and corrosion resistance
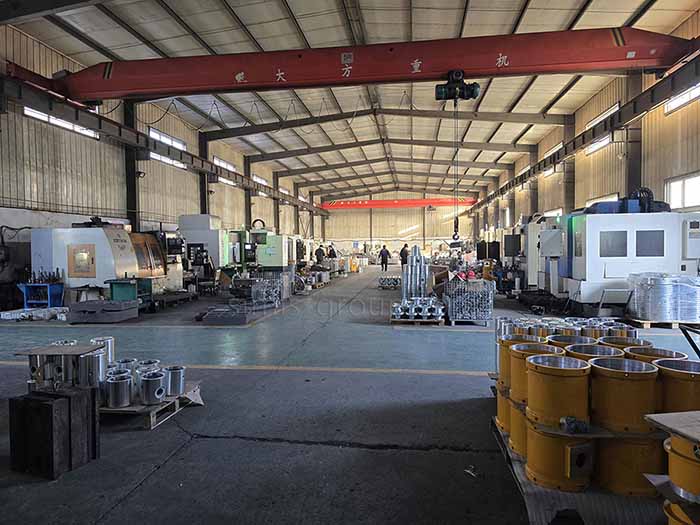
Machining
Machining is a post-processing process for steel forings, which improves the accuracy, surface quality and functionality of forgings through fine processing.
· Optimize appearance quality
· Improve part structure and function
· Process thin walls and complex shapes
Different Materials Of Forging Steel
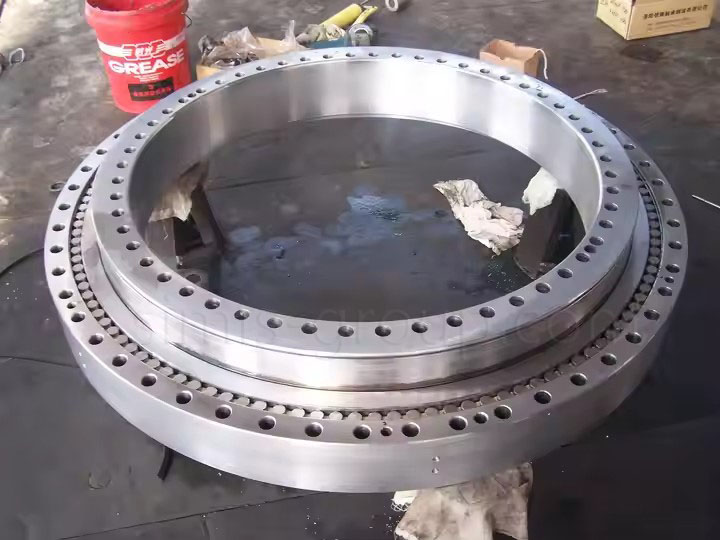
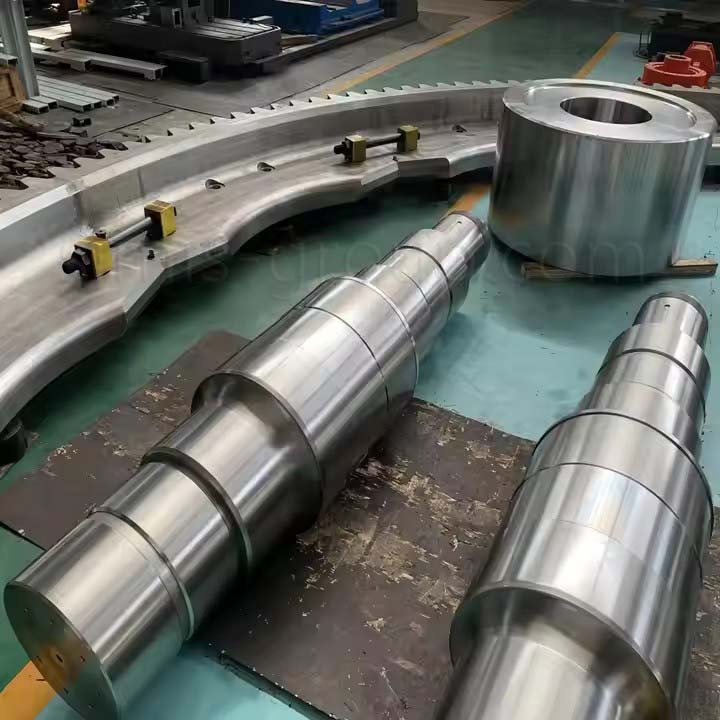
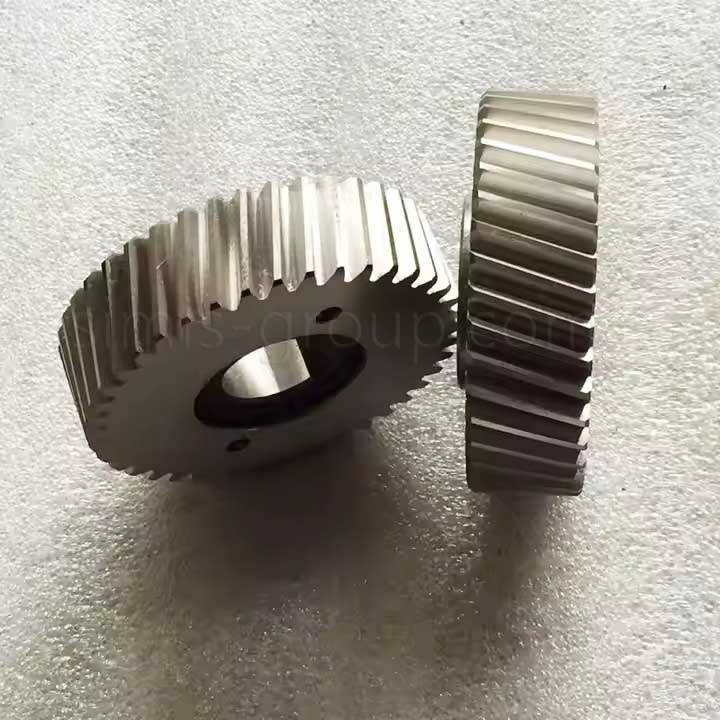
1. Carbon steel
According to the carbon content, it is divided into low carbon steel, medium carbon steel and high carbon steel.
· Low carbon steel (carbon content ≤ 0.25%):
good plasticity, toughness and weldability, low strength, used for forging mechanical parts, shafts, gears. Common grades: AISI 1018, 1020, Q235.
· Medium carbon steel (carbon content 0.25% ~ 0.60%): high strength, hardness and wear resistance, moderate plasticity, used for forging gears, shafts, connecting rods, high-strength bolts. Common grades: AISI 1045, 4140, 4340.
· High carbon steel (carbon content ≥ 0.60%): high hardness, high wear resistance, but low plasticity and toughness, used for cutting tools, springs, high-strength parts. Common grades: AISI 1060, 1095.
2. Alloy steel
Alloy steel is made by adding appropriate amounts of alloying elements (such as chromium, nickel, molybdenum, manganese, etc.) to carbon steel to improve strength, toughness, heat resistance and corrosion resistance.
· Low alloy steel: higher strength and toughness, good weldability, used for forging aerospace parts, automotive parts, and oil drilling equipment.
Common grades: AISI 4130, 4140, 4340.
·High alloy steel: excellent corrosion resistance, heat resistance and wear resistance, used to manufacture chemical equipment, molds, and high-temperature parts.
Common grades: AISI 304, 316, H13.
3. Stainless steel
Stainless steel has excellent corrosion resistance and is often used in special environments.
· Austenitic stainless steel: good corrosion resistance, plasticity and toughness, non-magnetic, used for forging chemical equipment, food processing equipment, and medical equipment.
Common grades: AISI 304, 316.
· Martensitic stainless steel: high hardness, high strength, moderate corrosion resistance, used for forging tools, bearings, and pump shafts.
Common grades: AISI 410, 420.
· Duplex stainless steel: It has the advantages of both austenite and ferrite, high strength and good corrosion resistance, and is used to forge marine engineering and chemical equipment parts.
Common grades: 2205, 2507.
4. Special purpose forged steel
· Heat-resistant steel: High temperature resistance and oxidation resistance, used to manufacture aircraft engines and gas turbines.
Common grades: Inconel 718, Hastelloy.
· Wear-resistant steel: High hardness and high wear resistance, used to manufacture mining machinery parts and engineering machinery parts.
Common grades: AR400, AR500.
1. Carbon steel
According to the carbon content, it is divided into low carbon steel, medium carbon steel and high carbon steel.
· Low carbon steel (carbon content ≤ 0.25%):
good plasticity, toughness and weldability, low strength, used for forging mechanical parts, shafts, gears. Common grades: AISI 1018, 1020, Q235.
· Medium carbon steel (carbon content 0.25% ~ 0.60%): high strength, hardness and wear resistance, moderate plasticity, used for forging gears, shafts, connecting rods, high-strength bolts. Common grades: AISI 1045, 4140, 4340.
· High carbon steel (carbon content ≥ 0.60%): high hardness, high wear resistance, but low plasticity and toughness, used for cutting tools, springs, high-strength parts. Common grades: AISI 1060, 1095.
2. Alloy steel
Alloy steel is made by adding appropriate amounts of alloying elements (such as chromium, nickel, molybdenum, manganese, etc.) to carbon steel to improve strength, toughness, heat resistance and corrosion resistance.
· Low alloy steel: higher strength and toughness, good weldability, used for forging aerospace parts, automotive parts, and oil drilling equipment.
Common grades: AISI 4130, 4140, 4340.
·High alloy steel: excellent corrosion resistance, heat resistance and wear resistance, used to manufacture chemical equipment, molds, and high-temperature parts.
Common grades: AISI 304, 316, H13.
3. Stainless steel
Stainless steel has excellent corrosion resistance and is often used in special environments.
· Austenitic stainless steel: good corrosion resistance, plasticity and toughness, non-magnetic, used for forging chemical equipment, food processing equipment, and medical equipment.
Common grades: AISI 304, 316.
· Martensitic stainless steel: high hardness, high strength, moderate corrosion resistance, used for forging tools, bearings, and pump shafts.
Common grades: AISI 410, 420.
· Duplex stainless steel: It has the advantages of both austenite and ferrite, high strength and good corrosion resistance, and is used to forge marine engineering and chemical equipment parts.
Common grades: 2205, 2507.
4. Special purpose forged steel
· Heat-resistant steel: High temperature resistance and oxidation resistance, used to manufacture aircraft engines and gas turbines.
Common grades: Inconel 718, Hastelloy.
· Wear-resistant steel: High hardness and high wear resistance, used to manufacture mining machinery parts and engineering machinery parts.
Common grades: AR400, AR500.
Application Of Steel Forging
Steel Forging Parts Custom
Steel Forging Company's Custom Steps
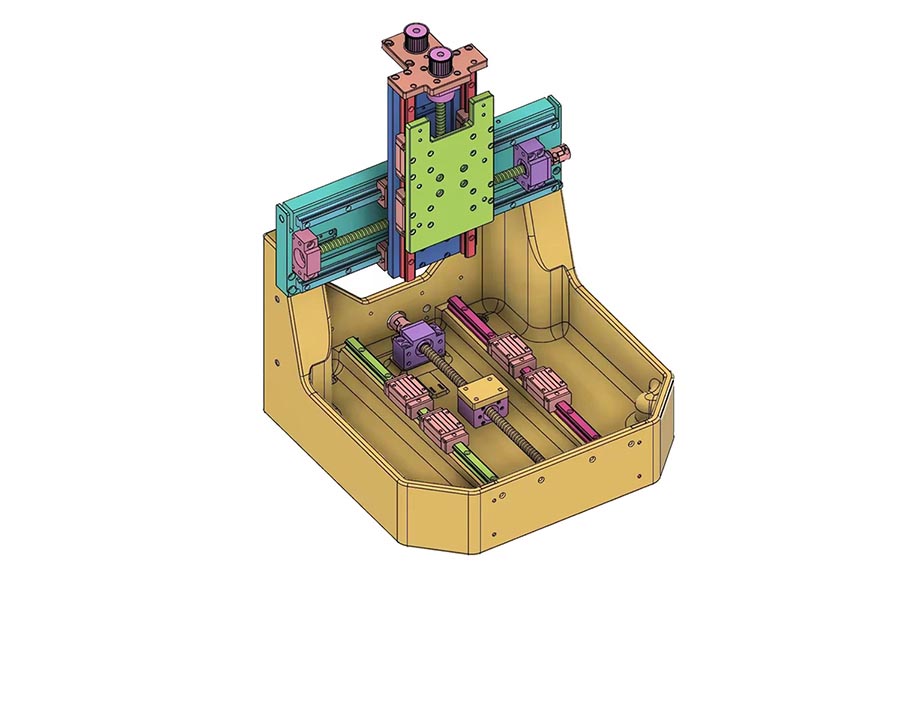
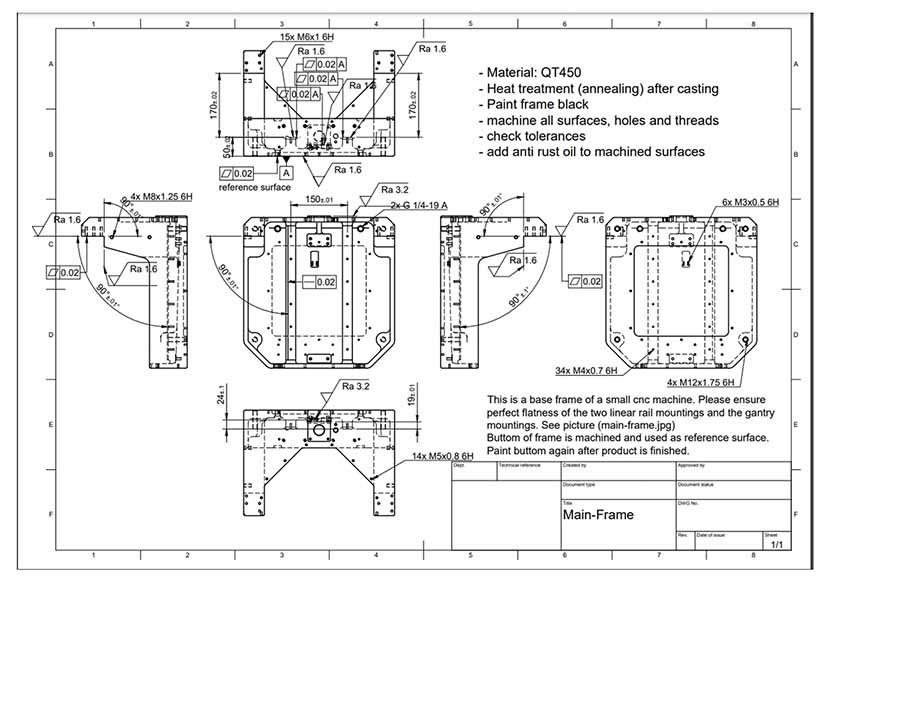
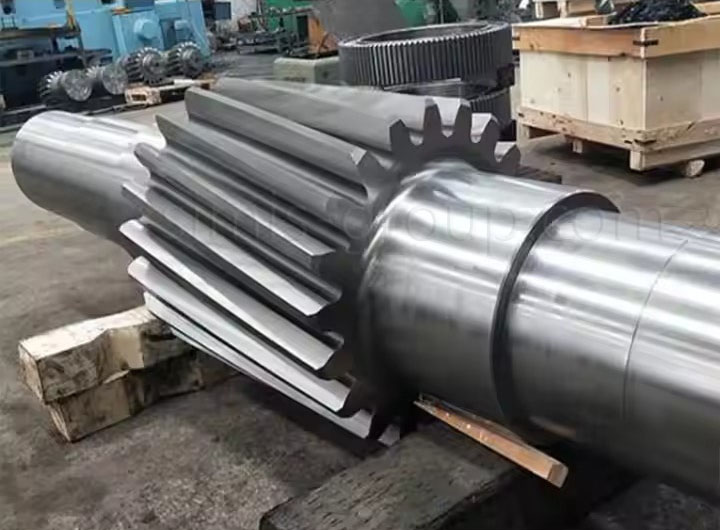
Confirm customization requirements
1. Provide detailed design documents or samples of parts
The Simis engineering team will analyze the 3D drawings (CAD models) and processing drawings of forgings provided by customers to ensure that they meet the manufacturing requirements.
Samples: If customers can provide samples, we can also forge and replicate them according to the samples.
2. Confirm the performance requirements of steel forgings
Clearly define the various performance requirements of forgings, such as strength, hardness, wear resistance, corrosion resistance, etc., and confirm the surface roughness, appearance quality, dimensional tolerance and accuracy requirements of forgings.
3. Confirm the forging material
Select the appropriate forging material according to the use environment, technical requirements or customer requirements of the parts. Simis will give reasonable suggestions based on the price, mechanical properties, wear resistance, corrosion resistance, etc. of the material.
4. Confirm the steel forging process
Determine the appropriate steel forging process based on the price, shape, size, accuracy, material, etc. of the parts.
5. Make samples
Forge the selected forging materials through the corresponding process to produce the first batch of samples.
6. Comprehensive inspection of samples
The produced samples will be fully inspected to ensure that they meet the design standards and customer quality requirements.
Dimension and tolerance inspection, performance testing, chemical composition analysis, non-destructive testing and other test reports
Production and quality control
7. Mass production
After the sample is confirmed and approved by the customer, the mass production schedule is arranged according to the order requirements, and the production materials are prepared. The same forging equipment and process as the sample stage are used in the mass production process.
8. Mass production quality control
We implement strict quality control measures during the production process to ensure that the quality of each steel forgings in mass production meets customer requirements. During the production process, the size, appearance, physical properties, etc. of the steel forgings are regularly inspected to ensure the consistency of each batch of parts.
9. Post-production product quality inspection
Multiple inspections by multiple people: We will arrange different inspectors to conduct multiple random inspections on the final product, including dimensional accuracy, surface quality, strength, hardness, etc., to ensure that the steel parts produced meet customer requirements.
10. Parts packaging and delivery
Packaging: Pack and ship the parts that have passed the quality inspection, and select the appropriate packaging method and the appropriate logistics method (such as air, sea, and land transportation) to deliver them to customers on time.
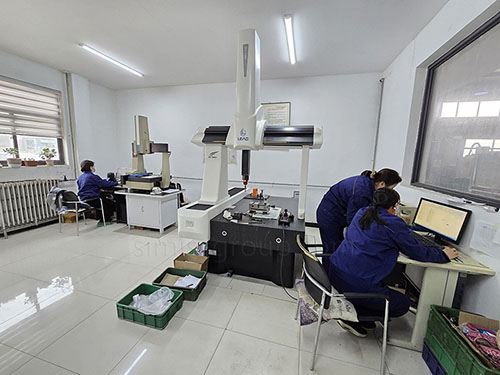
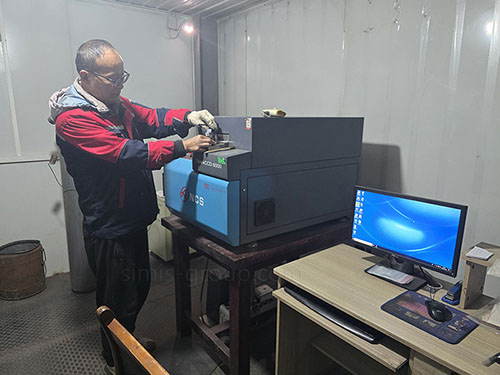
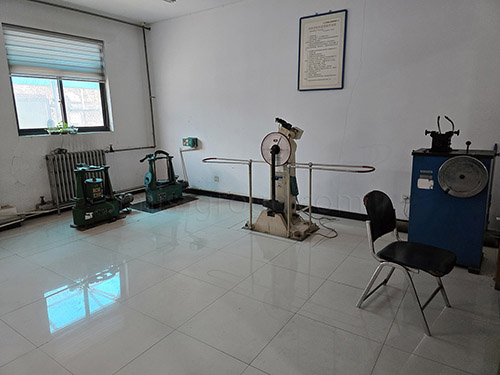
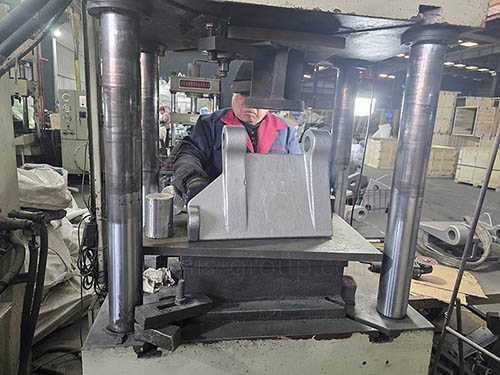
If you want to custom parts, please send me the design drawings and 3D drawings of theparts you want to customize by email, and we will calculate an accurate price for you bylooking at the detailed part parameters and 3D model.