Simis Gravity Permanent Mold Casting Foundry
Gravity Permanent Mold Casting Factory Introduction
SIMIS Gravity Permanent Mold Casting Factory focuses on the production of gravity casting parts, providing high-quality gravity permanent mold castings of aluminum alloys, copper alloys and other metal materials for the automotive, aerospace, engineering machinery, electronic equipment and other industries.
Simis Gravity Permanent Mold Casting Plant produces about 6,000 tons of castings annually. It has several advanced gravity permanent mold casting production lines and complete auxiliary processing equipment, including: gravity casting machines, automatic pouring systems, melting equipment, CNC machining centers, etc., to meet the production needs of small and medium-sized and complex castings. It can cast engine housings, hydraulic valve bodies, motor housings, radiators, cylinder heads and other complex precision parts. We serve global customers with high-quality castings and efficient production capabilities.
Gravity Permanent Mold Casting Process
Gravity permanent mold casting process overview
Gravity casting uses gravity to pour molten metal into a pre-prepared metal model, and forms a casting after cooling and solidification. Gravity casting is suitable for producing castings with high precision and simple structure, and has the characteristics of low cost and easy operation.
1. Mold preparation
Gravity casting molds are made of sand molds, metal or ceramic materials.
The design process of the mold needs to consider factors such as the fluidity of the metal, the cooling rate and the complex shape of the casting.
2. Melting metal materials
The metal material is heated to above its melting point in a high-temperature furnace to completely melt the metal material.
3. Pouring
During the pouring process, the molten metal flows from the metal molten pool into the runner system of the mold by gravity, enters the mold cavity through the gate, fills the mold cavity and forms the shape of the desired casting.
4. Cooling and solidification
After entering the mold cavity, the molten metal begins to cool and solidify, gradually forming a casting.
5. Gravity permanent mold castings demolding
After the casting is completely cooled, disassemble or destroy the mold and remove the casting from the mold.
6. Castings cleaning
The casting removed from the mold is cleaned, the excess gates, risers and other accessories on the surface are removed, and further processing or inspection is performed.
7. Post-processing and testing
After demoulding and cleaning, the casting needs to go through post-processing steps such as heat treatment and machining to improve the performance of the casting and meet the customer's design requirements.
8. Quality Inspection
Comprehensive measurement is carried out through surface quality inspection, dimension inspection, mechanical property test and other quality inspection methods to ensure that permanent mold castings meet the requirements of design drawings.
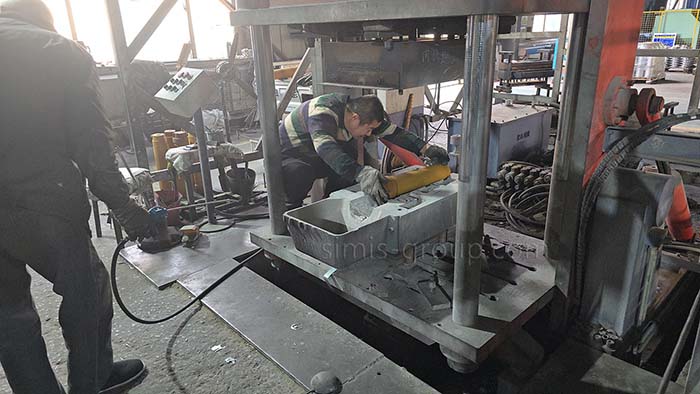
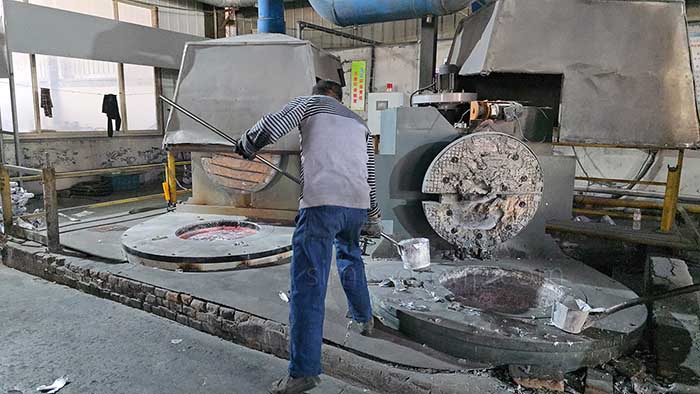
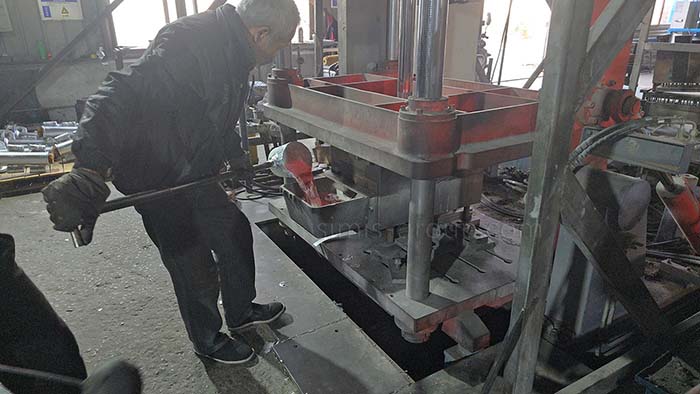
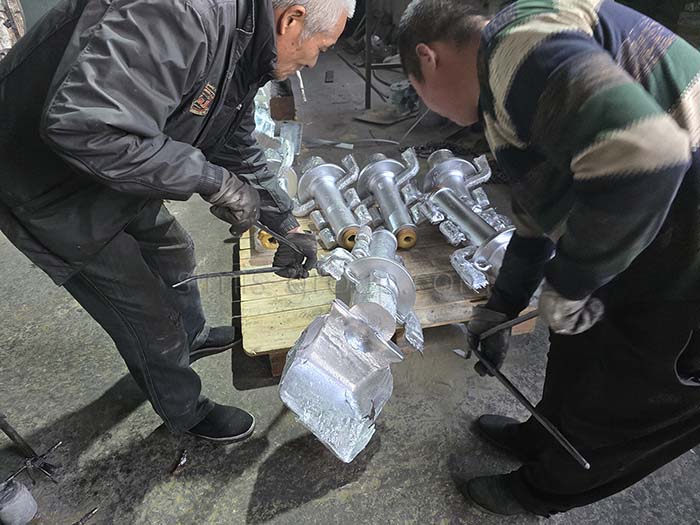
Materials For Gravity Casting
What metal parts can be cast in Simis Gravity Permanent Mold Casting Factory?
Simis gravity casting foundry gravity permanent mold mainly uses aluminum alloy, zinc alloy, magnesium alloy and copper alloy for the manufacture of street lamp housing, decorative lamp holder, cylinder head, radiator, pump cover, turbine housing and other lightweight metal parts.
1. Aluminum Alloys:
·Aluminum-Silicon Alloys
·Aluminum-Magnesium Alloys
·Aluminum-Zinc Alloys
·Aluminum-Copper Alloys
·Aluminum-Manganese Alloys
·Aluminum-Titanium Alloys
· …
2. Other metal Alloys:
·Brass
·Bronze
·Nickel alloys
·Titanium alloys
·Copper alloy
·Magnesium alloy
·Zinc alloy
·…
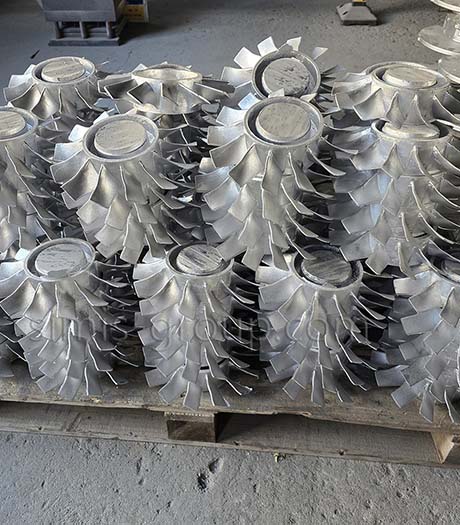
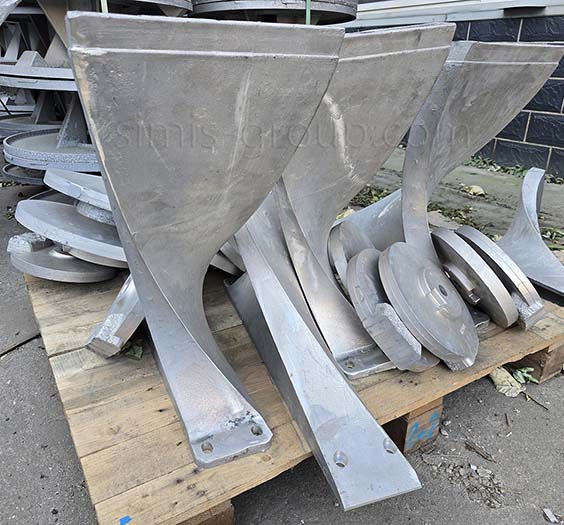
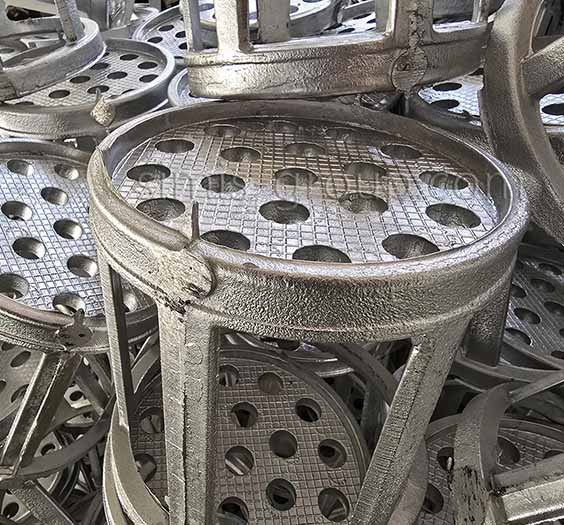
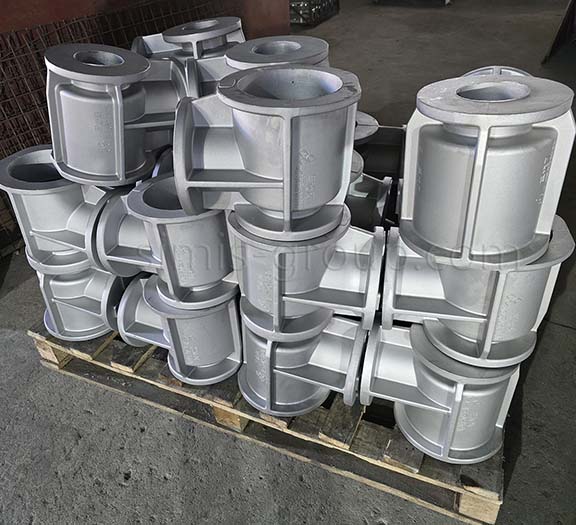