Steel Casting Company's Process
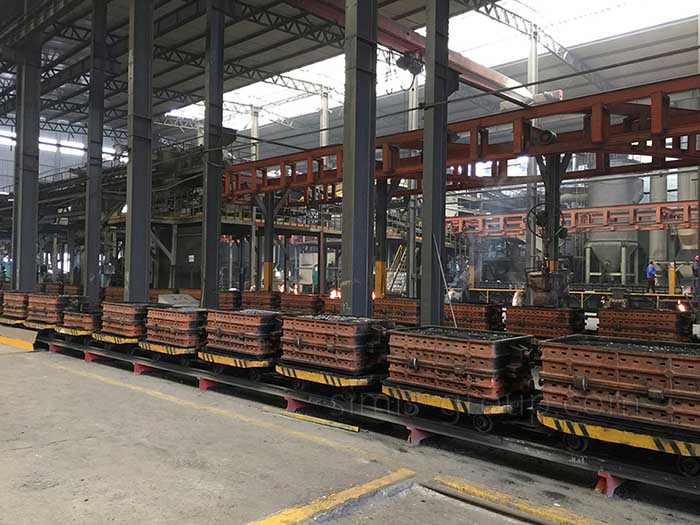
Sand Casting
Sand casting uses sand as the casting material, then pours molten steel into the casting mold, takes out the casting after cooling, cleans and performs post-processing.
· The mold manufacturing cost is low and can be used many times
· Can cast large and medium-sized steel castings with complex shapes and large sizes.
· Suitable for small, medium and large batch production.

Investment Casting
Investment casting uses soluble or combustible casting molds (such as wax molds) to make castings, and is often used to make steel parts with complex shapes and high precision requirements.
· High surface quality
· No need for a lot of post-processing
· Suitable for small batches and high precision steel parts
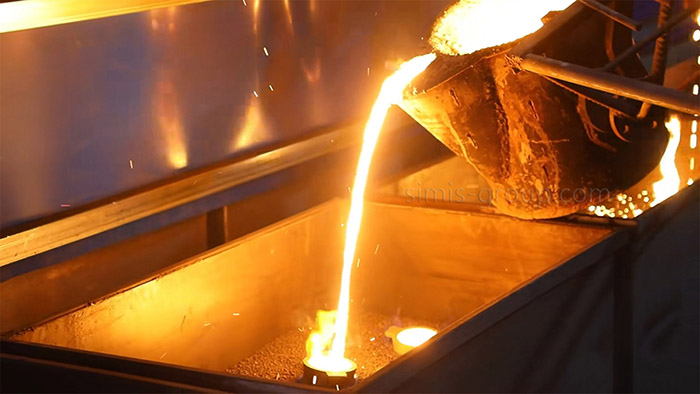
Shell Mold Casting
Shell casting uses ceramics or other refractory materials as casting molds, and the casting mold is usually made by applying multiple layers of refractory coatings on the surface of the model.
· Suitable for small batches or high-value steel castings
· Used to produce small and medium-sized steel castings
· Make complex steel castings
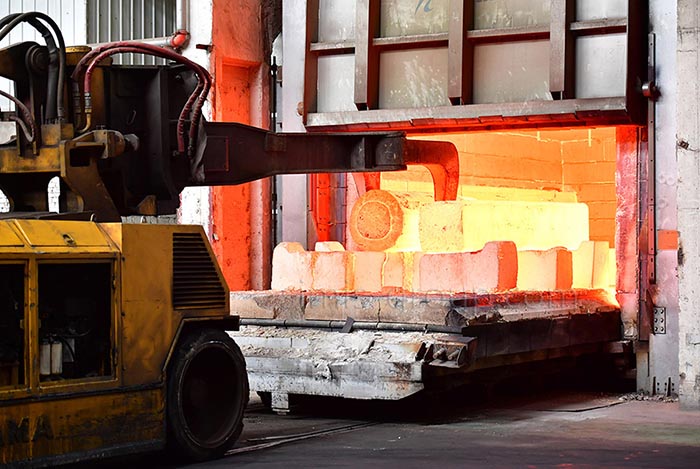
Heat Treatment
Heat treatment is to change the internal structure and properties of steel materials by heating, insulation, cooling, etc., improve the mechanical properties of metals, extend service life, and optimize processing performance.
· Improve the hardness and strength of steel materials
· Improve the toughness of steel materials
· Improve wear resistance and corrosion resistance

Machining
Mechanical machining is a post-processing process for castings. Through fine machining, the accuracy, surface quality and functionality of steel castings are improved.
· Optimize appearance quality
· Improve cast steel part structure and function
· Process thin walls and complex shapes
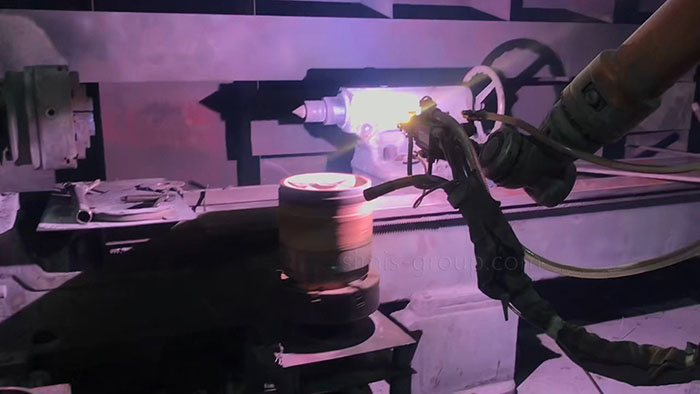
Surface Treatment
Surface treatment can change the surface of castings by physical, chemical or mechanical methods to improve the surface quality of steel castings, increase their durability, and improve appearance and functionality.
· Improve surface hardness
· Improve appearance and improve dimensional accuracy
· Improve adhesion and corrosion resistance
Different Materials Of Casting Steel
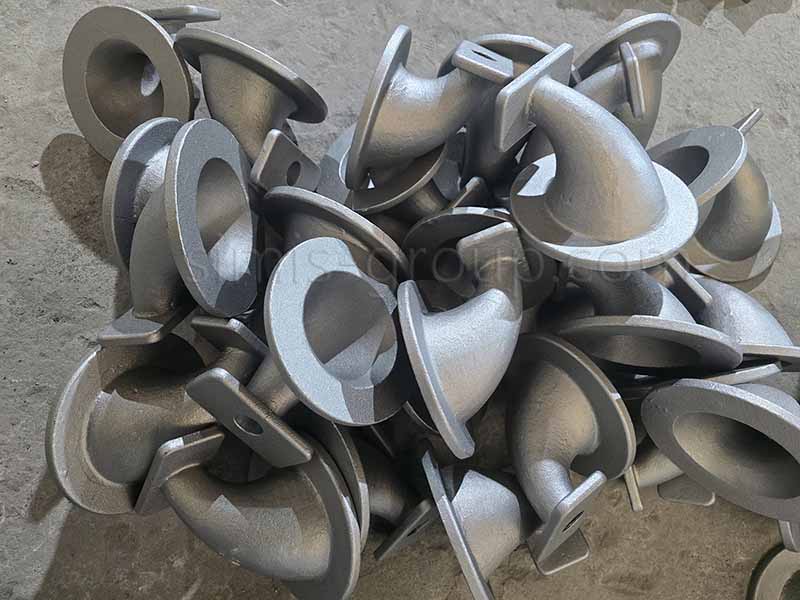
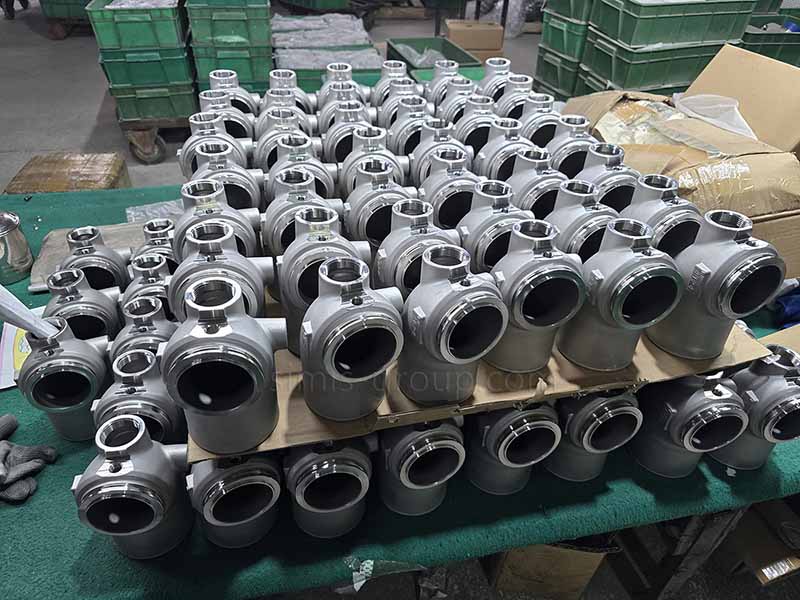
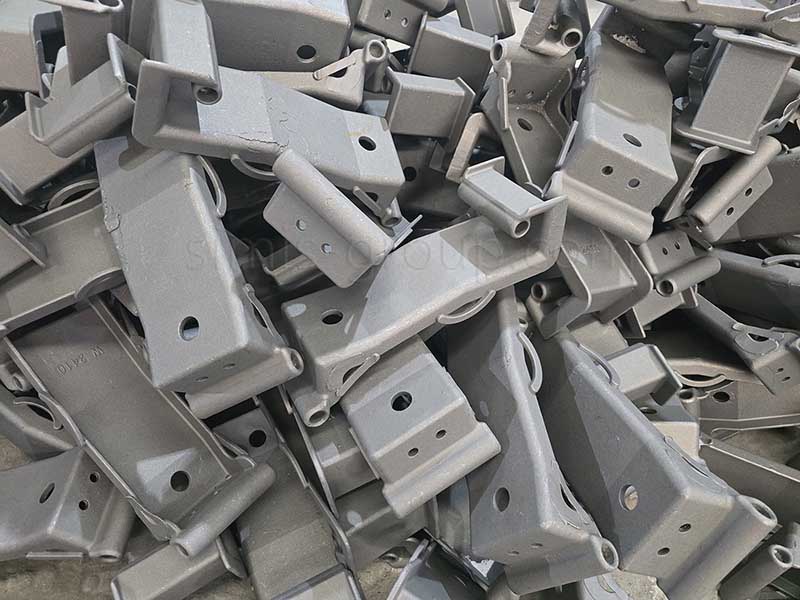
1. Carbon steel
Steels with different carbon contents have different mechanical properties and uses.
· Low carbon steel (carbon content ≤ 0.25%):
Used to manufacture parts that do not require high strength and toughness, such as racks, bearing seats, etc.
· Medium carbon steel (carbon content 0.25% to 0.60%):
Used to manufacture parts that require certain strength and toughness, such as gears, shafts, connecting rods, etc.
· High carbon steel (carbon content ≥ 0.60%):
Used to manufacture parts with high strength and hardness, such as tools, molds, etc.
2. Alloy steel
Alloy steel is made by adding appropriate amounts of alloying elements (such as chromium, nickel, molybdenum, manganese, etc.) to carbon steel to improve the strength, hardness, toughness, corrosion resistance or high temperature resistance of steel materials.
· Low alloy steel: commonly used in machinery and engineering equipment, such as ZG35CrMo, ZG40Mn,
· High alloy steel: commonly used in high temperature and high pressure containers and key components, such as ZG12CrMoV, ZG40CrNiMo.
· Wear-resistant alloy steel: used for crusher liners, excavator bucket teeth, etc., such as high manganese steel (ZG13Mn13).
3. Stainless steel
Stainless steel has high corrosion resistance, good mechanical properties and strong oxidation resistance.
· Austenitic stainless steel (such as ZG304, ZG316):
The best corrosion resistance, used for chemical and food industry equipment.
· Martensitic stainless steel (such as ZG410, ZG420):
High wear resistance, used for knives, pump shafts, etc.
· Ferritic stainless steel (such as ZG430):
Good stress corrosion resistance, used in low-load corrosion-resistant environments.
· Duplex stainless steel (such as ZG2205):
Has both austenitic and ferritic properties, used in ships, chemical equipment, etc.
4. Tool steel
Tool steel has a high carbon content and high alloying elements. It is a cast steel material characterized by high hardness and wear resistance. It is specially used to manufacture tools, molds and other steels that require high hardness, wear resistance, heat resistance, impact resistance and machinability.
· Cold work tool steel (such as Cr12MoV):
Used for stamping dies, cold shears, etc.
· Hot work tool steel (such as H13, ZG4Cr5MoSiV):
Used for casting dies and forging dies working under high temperature conditions.
· High speed tool steel (such as W18Cr4V):
Used for cutting tools and high speed machining tools.
1. Carbon steel
Steels with different carbon contents have different mechanical properties and uses.
· Low carbon steel (carbon content ≤ 0.25%):
Used to manufacture parts that do not require high strength and toughness, such as racks, bearing seats, etc.
· Medium carbon steel (carbon content 0.25% to 0.60%):
Used to manufacture parts that require certain strength and toughness, such as gears, shafts, connecting rods, etc.
· High carbon steel (carbon content ≥ 0.60%):
Used to manufacture parts with high strength and hardness, such as tools, molds, etc.
2. Alloy steel
Alloy steel is made by adding appropriate amounts of alloying elements (such as chromium, nickel, molybdenum, manganese, etc.) to carbon steel to improve the strength, hardness, toughness, corrosion resistance or high temperature resistance of steel materials.
· Low alloy steel: commonly used in machinery and engineering equipment, such as ZG35CrMo, ZG40Mn,
· High alloy steel: commonly used in high temperature and high pressure containers and key components, such as ZG12CrMoV, ZG40CrNiMo.
· Wear-resistant alloy steel: used for crusher liners, excavator bucket teeth, etc., such as high manganese steel (ZG13Mn13).
3. Stainless steel
Stainless steel has high corrosion resistance, good mechanical properties and strong oxidation resistance.
· Austenitic stainless steel (such as ZG304, ZG316):
The best corrosion resistance, used for chemical and food industry equipment.
· Martensitic stainless steel (such as ZG410, ZG420):
High wear resistance, used for knives, pump shafts, etc.
· Ferritic stainless steel (such as ZG430):
Good stress corrosion resistance, used in low-load corrosion-resistant environments.
· Duplex stainless steel (such as ZG2205):
Has both austenitic and ferritic properties, used in ships, chemical equipment, etc.
4. Tool steel
Tool steel has a high carbon content and high alloying elements. It is a cast steel material characterized by high hardness and wear resistance. It is specially used to manufacture tools, molds and other steels that require high hardness, wear resistance, heat resistance, impact resistance and machinability.
· Cold work tool steel (such as Cr12MoV):
Used for stamping dies, cold shears, etc.
· Hot work tool steel (such as H13, ZG4Cr5MoSiV):
Used for casting dies and forging dies working under high temperature conditions.
· High speed tool steel (such as W18Cr4V):
Used for cutting tools and high speed machining tools.
Application Of Steel Castings
Steel Casting Parts Custom
Steel Castings Company's Custom Steps
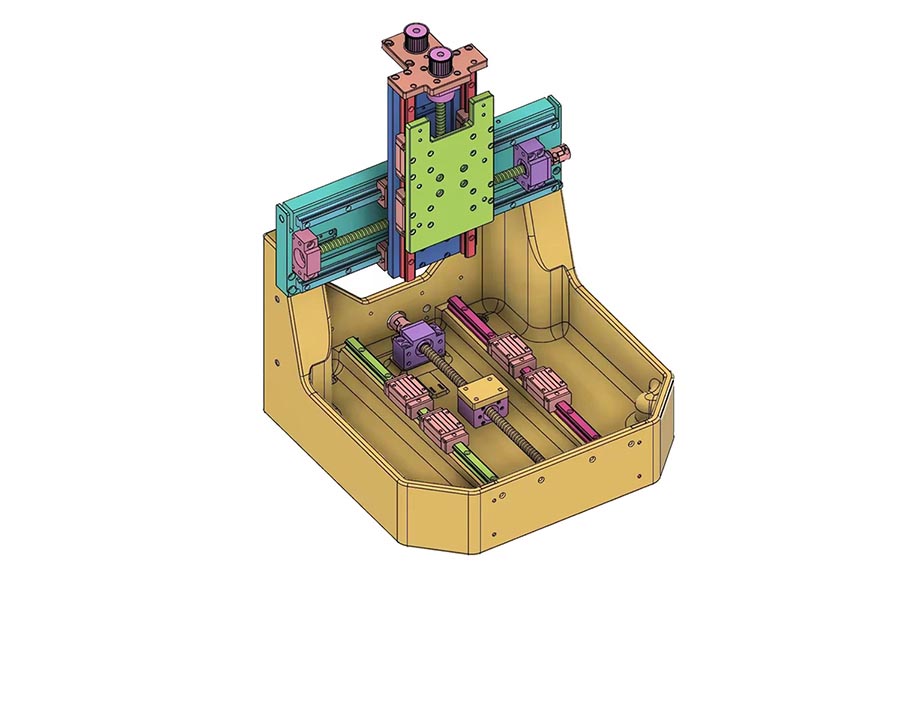
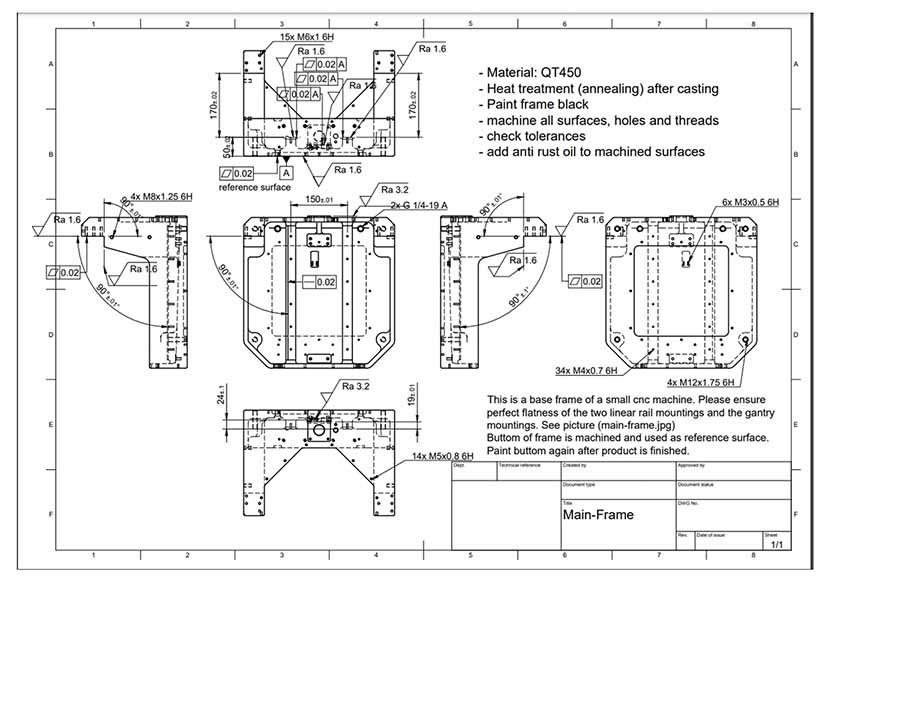
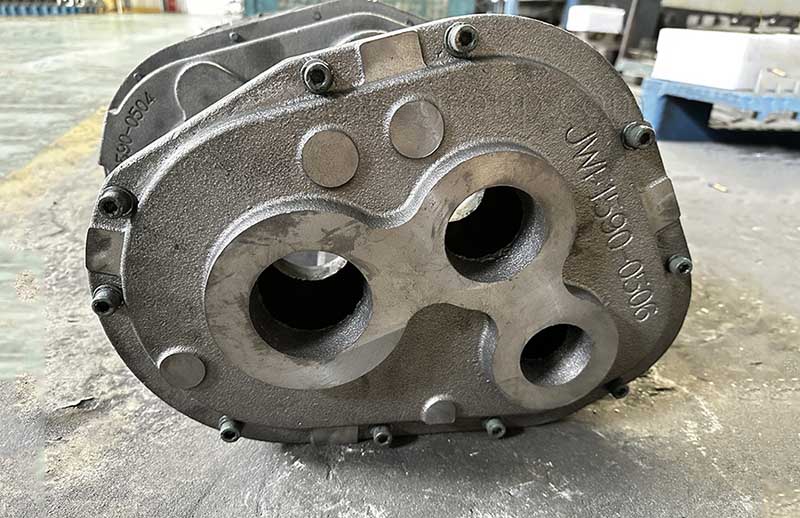
Confirm customization requirements
1. Provide detailed design documents or samples of parts
The engineering team will review the 3D drawings (CAD models) and corresponding processing plans provided by customers to ensure that they meet manufacturing requirements.
Samples: If customers provide samples, we can also produce according to samples.
2. Confirm the material of the steel casting
Choose the appropriate cast steel material according to the use environment, technical requirements or customer requirements of the parts. We will give reasonable suggestions based on the price, mechanical properties, wear resistance, corrosion resistance, etc. of the materials.
3. Confirm the casting process
Determine the appropriate steel casting process based on customer needs and part price, shape, size, precision, material, etc.
4. Confirm the requirements for various product attributes
Confirm the various performance requirements of the parts under the casting process and materials, such as strength, hardness, wear resistance, corrosion resistance, etc.
According to the drawings and product requirements, confirm the dimensional tolerance and precision requirements, surface roughness, appearance quality and other requirements of the product.
5. Make molds and samples
Make casting molds that meet the requirements according to the drawings or samples provided by the customer; and cast the selected casting materials through the corresponding process to produce the first batch of samples
6. Comprehensive inspection of samples
The produced steel casting samples will be fully inspected, including size and tolerance inspection, performance test, chemical composition analysis, non-destructive testing and other test reports.
7. Mass production
After the samples are confirmed and approved by the customer, arrange the mass production plan according to the order requirements and prepare the production materials.
Production and quality control
8. Quality control in mass production
We implement strict quality control measures during the production process to ensure that the quality of each steel casting in mass production meets customer requirements.
Production process quality monitoring: Regular sampling during the production process to check the size, appearance, physical properties, etc. of steel castings to ensure the consistency of each batch of parts.
Equipment inspection: Regularly inspect production equipment to avoid production deviations due to equipment failure.
9. Product quality inspection after production
Multiple inspections by multiple people: We will arrange different inspectors to conduct multiple random inspections on the final product, including dimensional accuracy, surface quality, strength, hardness, etc., to ensure that the parts produced meet customer requirements.
Quality inspection report: Provide a detailed quality inspection report for each steel casting inspected.
10. Parts packaging and delivery
Packaging: For parts that pass the quality inspection, pack and ship them, choose the appropriate packaging method and the appropriate logistics method (such as air, sea, and land transportation) to avoid damage during transportation and deliver them to customers on time.
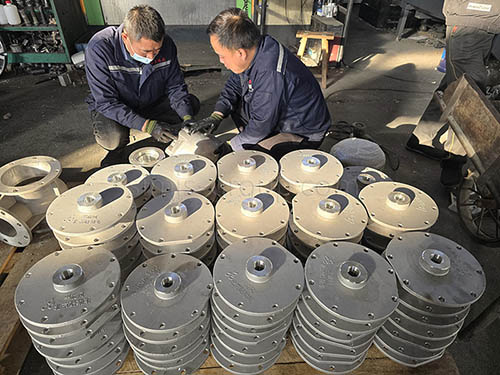
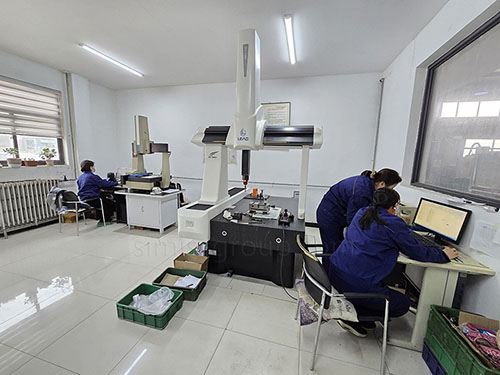
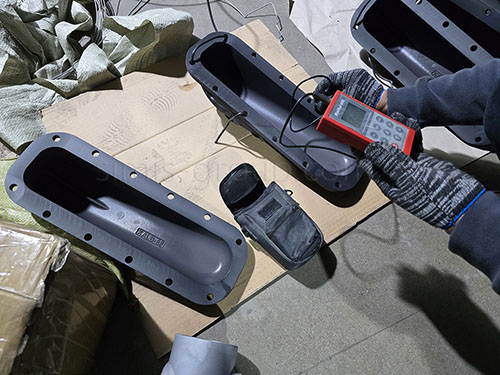
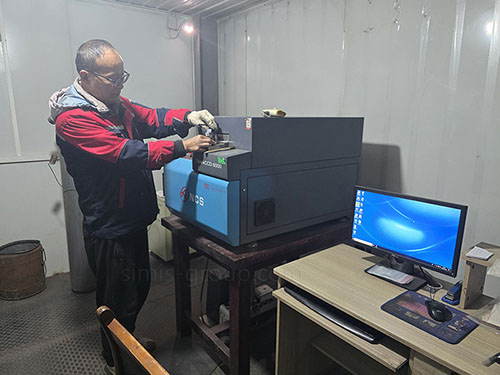
If you want to custom parts, please send me the design drawings and 3D drawings of theparts you want to customize by email, and we will calculate an accurate price for you bylooking at the detailed part parameters and 3D model.