Simis Lost Foam Casting Foundry
Lost Foam Casting Factory Introduction
Simis Lost Foam Casting Foundry covers an area of about 13,000 square meters, with an annual casting capacity of 10,000-12,000 tons. It specializes in the production of medium and large complex structural castings made of various materials such as gray cast iron, ductile iron, stainless steel, carbon steel, aluminum alloy, etc., such as engine cylinder blocks, gearbox housings, pump bodies, valve bodies, rail transit components, etc. The weight of a single casting can reach 5 tons, and it widely serves the automotive, construction machinery, rail transit, mining equipment and other industries.
The foundry is equipped with multiple automated production lines and advanced casting equipment, including 15 foam molding machines (with a maximum model size of up to 3 meters), 12 melting furnaces, 5 fully automatic dry sand regeneration and recycling systems, multiple automated production lines and advanced CNC machining centers to support the efficient production of medium and large structural parts and ensure product quality and production efficiency.
Lost Foam Casting Process
Lost Foam Casting process overview
Lost Foam Casting is a precision casting process that makes a mold of expandable foam plastic (such as polystyrene) in the same shape as the casting, assembles it, coats it with a high-temperature resistant coating, buries it in dry sand after drying, and then when pouring molten metal, the foam mold vaporizes and disappears due to heat, allowing the molten metal to fill the mold in place and finally solidify into shape. The Lost Foam Casting process has the advantages of high casting dimensional accuracy, good surface quality, reduced processing allowance and production cost, and is suitable for casting complex parts made of aluminum alloy, gray cast iron, ductile iron and steel.
1. Model making
Use expandable foam plastics such as polystyrene (EPS) to make a foam model with the same shape as the final casting through thermoforming, mold forming or extrusion.
In addition, the surface of the foam model needs to be carefully polished and trimmed by CNC machining, laser engraving, etc. to ensure that the model size is accurate and meets the design requirements and the surface quality requirements of the casting.
2. Apply high temperature resistant coating
A layer of high temperature refractory coating needs to be applied on the surface of the foam model. The main components of the coating usually include high temperature resistant sand, adhesive and water.
The coating process usually uses spraying, brushing or dipping to ensure that the coating is evenly covered on the surface of the foam model.
The coating is cured and has sufficient strength by natural drying or hot air drying.
3. Model embedding and sand mold making
The foam model coated with coating is placed in dry sand, and the sand is usually dry sand without binder.
Through vibration or compaction, the sand is tightly wrapped around the model to form a sand mold.
4. Model baking and mold preheating
Before pouring, the foam model needs to be properly baked to improve the strength of the coating and avoid the impact caused by rapid gasification when the molten metal is poured.
The sand mold should be preheated. Preheating the sand mold helps to improve the fluidity of the molten metal, reduce thermal shock, and effectively avoid surface defects of lost foam castings.
5. Melting metal and pouring
According to the material requirements of the casting, select suitable metals (such as aluminum alloy, cast iron, steel, etc.) for melting.
The molten metal is injected into the sand mold through the pouring system (such as gate, riser, etc.). Since the model is a foam plastic, when the temperature of the molten metal reaches a certain level, the foam will quickly gasify and disappear to form a cavity. The molten metal fills the cavity and finally solidifies and forms.
6. Cooling and demolding of castings
After the molten metal fills the model, it needs to wait for it to cool naturally. The metal will solidify during the cooling process and gradually form a casting.
After the metal is completely cooled, open the sand mold, remove the sand shell and take out the casting. Since the foam model is completely vaporized and disappears, there is no need for traditional mold removal.
7. Casting cleaning and post-processing
After the lost foam casting is taken out of the sand mold, the surface needs to be cleaned, and the residual sand shell and coating are removed by shot blasting, sand blasting or mechanical cleaning.
Post-processing: The casting may require finishing, such as grinding, cutting, heat treatment, etc., to ensure that the casting meets the size, tolerance and mechanical property requirements.
8. Quality inspection
Inspection link: After the casting is cleaned, the size inspection, hardness test, mechanical property test, etc. are carried out to ensure that it meets the design and use requirements.
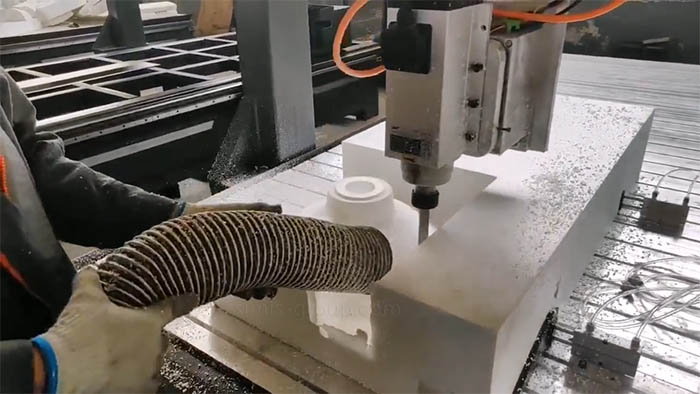
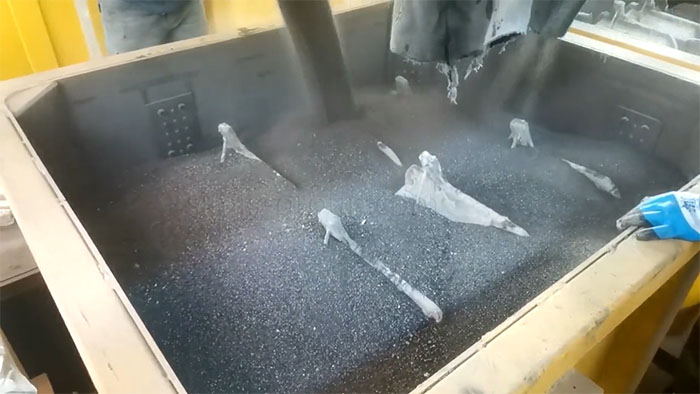
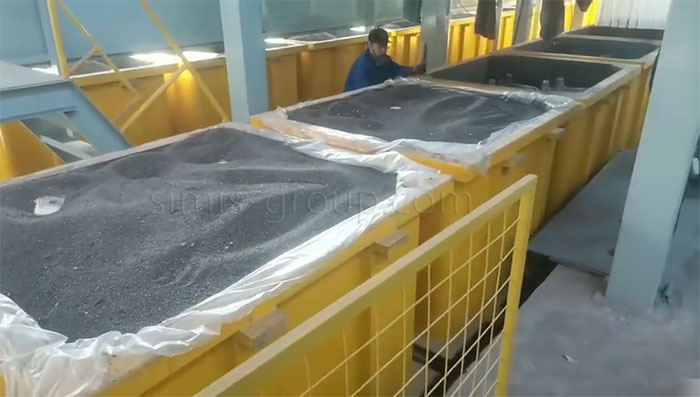
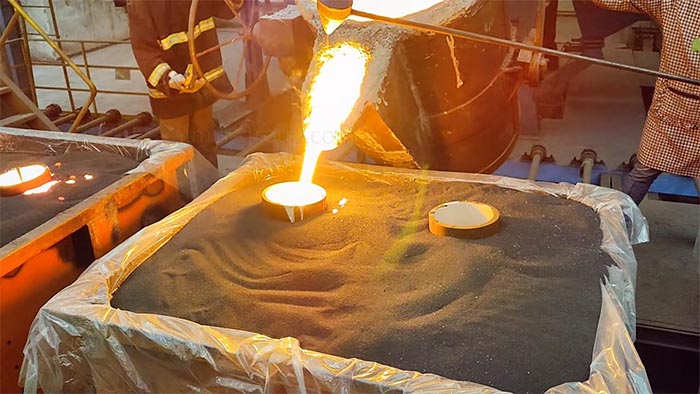
Materials For Lost Foam Casting
What metal parts can be cast in Simis lost foam casting factory?
The materials commonly used by Simis Lost Foam Casting Factory are mainly aluminum alloy, cast iron, carbon steel, stainless steel, etc. Aluminum alloy is light in weight and has good corrosion resistance; gray cast iron and ductile iron have good casting and mechanical properties; carbon steel and stainless steel are mostly used for industrial equipment and mechanical parts with high requirements for strength and corrosion resistance; copper alloy is mainly used for parts with high requirements for conductivity and wear resistance.
1. Cast Iron
·Gray (Grey) Iron
·Ductile Iron
·Malleable cast iron
·Alloy Cast Iron:High chromium alloy cast iron, High nickel alloy cast iron, Silicon alloy cast iron, Aluminum alloy cast iron, …
2. Cast Steel
·Carbon Steel: Mild Steel, Medium Carbon Steel, High Carbon Steel,
·Alloy Steel: Low alloy steel, High alloy steel,
·Stainless Steel: Austenitic Stainless Steel, Ferritic Stainless Steel, Martensitic Stainless Steel, Duplex Stainless Steel, ...
3. Aluminum Alloys
·Aluminum-Silicon Alloys
·Aluminum-Magnesium Alloys
·Aluminum-Zinc Alloys
·…
4. Other Alloys
·Brass
·Bronze
·Nickel alloys
·Titanium alloys
·…
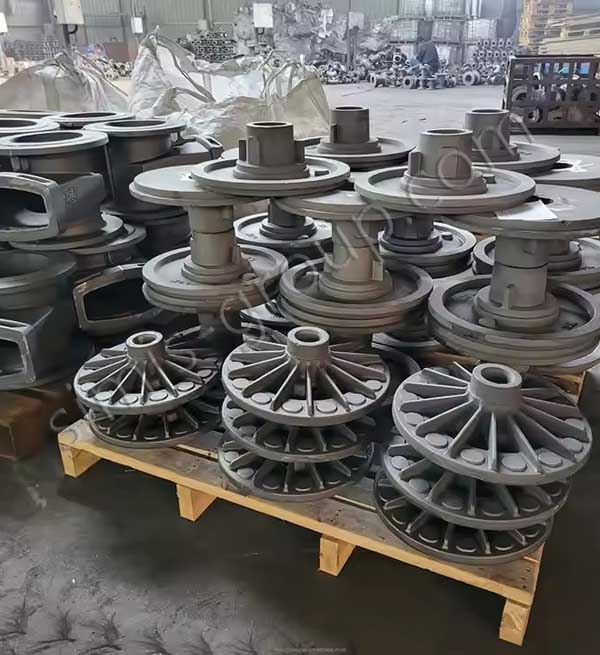
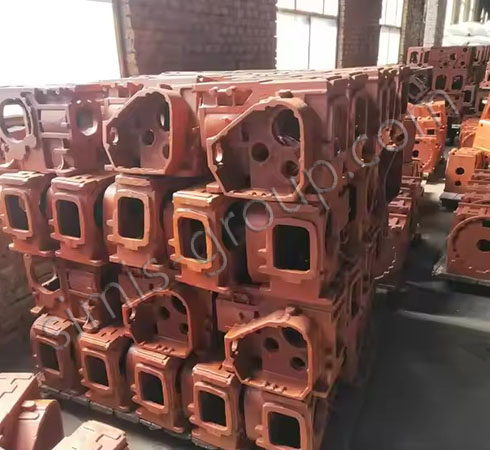
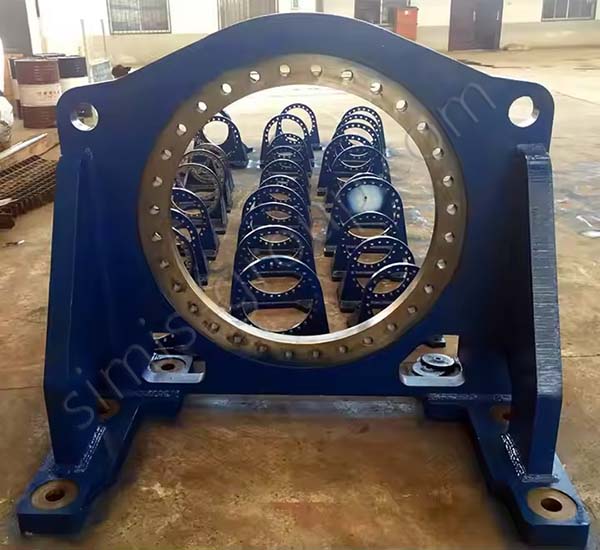
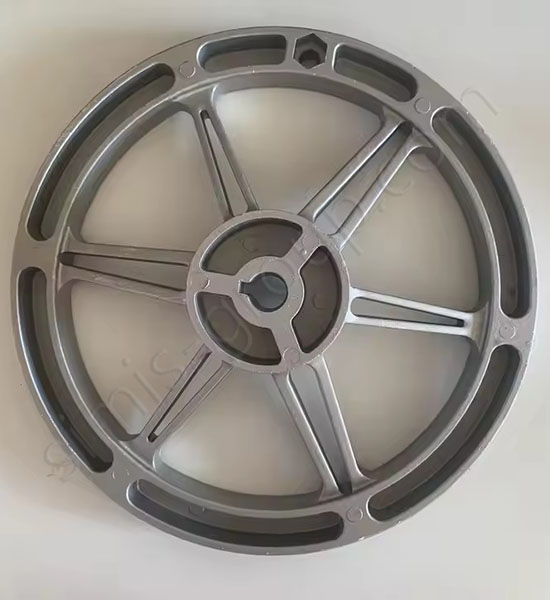