Simis Sand Casting Foundry
Simis Sand Casting Foundry Introduction
Simis Sand Casting Factory produces about 10,000 tons of castings annually, and customizes gray iron, ductile iron, alloy cast iron, carbon steel, stainless steel, alloy steel, aluminum alloy, copper alloy, titanium alloy and other metal material parts for automobiles, machinery, construction, energy, agriculture, industry and other fields.
Simis Sand Casting Foundry covers an area of about 15,000 square meters. The Foundry is equipped with modern equipment and automated production lines, such as fully automatic sand mold lines, automatic pouring systems and automated cleaning lines, melting furnaces, sand mold equipment, cleaning and post-processing equipment and other advanced casting equipment to ensure efficient and stable mass production.
The Foundry is also equipped with advanced testing equipment, such as three-coordinate measuring machines, spectrometers, hardness testers, etc., to accurately test castings to ensure that product quality meets customer standards.
Sand Casting Process
Sand casting process overview
Sand casting is to pour molten metal into a mold made of sand and a binder, and use the plasticity and good air permeability of the sand mold to form a casting. Sand casting is highly flexible and can cast castings with complex shapes and large sizes, with a relatively short production cycle.
1. Prepare sand mold
The basic raw materials for sand casting are river sand, silica sand or fine sand. Sand needs to be mixed with binders (such as bentonite, resin, clay, etc.) and additives (such as water, oil or other chemical additives).
(The two common sand molds are resin sand casting and clay sand casting)
Fill the mixed sand into the mold to form a sand mold.
2. Core making
The core is used for the internal space of the sand casting. It is generally made by mixing fine sand and binder and pressing. For castings with complex structures, cores are needed to form internal cavities or complex structures.
3. Mold closing and core loading
The upper and lower mold boxes of the sand mold are closed to form a complete casting.
The core is installed in the appropriate position before mold closing to ensure that the core does not shift during the pouring process, affecting the quality of the sand casting.
4. Pouring
The required metal material is melted at high temperature and enters the sand mold through the gate and riser. The molten metal flows into the mold cavity under the action of gravity, filling the entire space of the sand mold to form the initial shape of the sand casting.
5. Cooling and solidification
After the molten metal enters the sand mold, it begins to gradually cool and solidify into a solid state. The time required for the casting to cool and solidify in the sand mold is related to the size, shape and properties of the metal material.
6. Mold removal and sand casting cleaning
After the casting is completely cooled and solidified, disassemble the sand mold and take out the sand casting.
Remove sand particles, risers, gates, cores and other attachments on the surface of the casting.
7. Inspection and quality control
The cleaned castings usually need to be inspected for quality, such as size inspection, surface inspection, mechanical property testing, etc.
8. Post-processing
Heat treatment: Heat treatment (such as annealing, normalizing, quenching, etc.) is performed to improve the mechanical properties of sand castings and eliminate internal stress.
Processing: According to the needs of the casting, post-processing such as drilling, tapping, machining, etc. is carried out to achieve the final precision requirements.
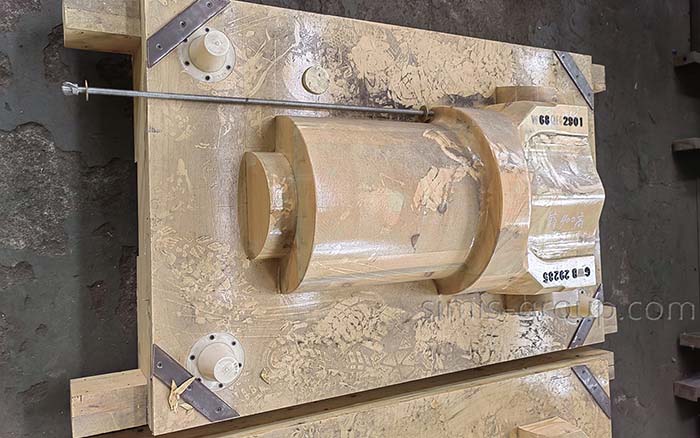
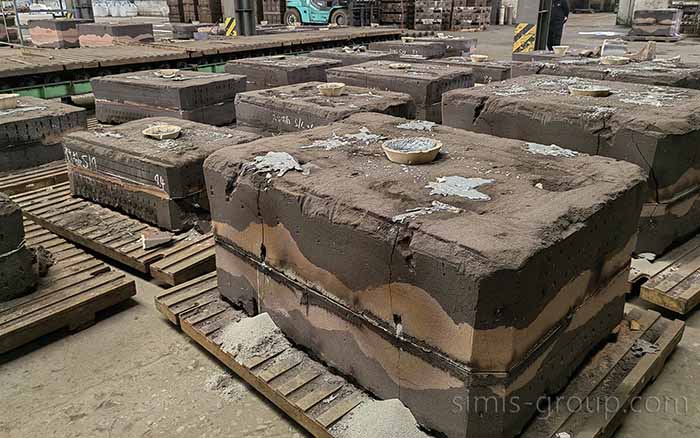
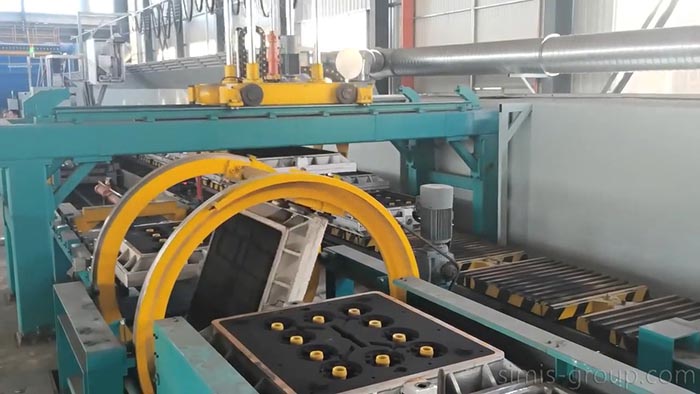
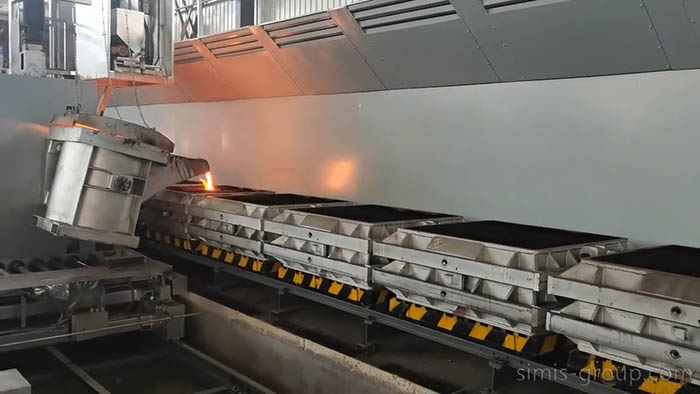
Materials For Sand Casting
What metal parts can be cast in Simis sand casting process?
Simis sand casting foundry can cast parts of various metal materials, including ferrous and non-ferrous metals, to meet customers' needs for castings with complex shapes, large sizes or special performance requirements. Common ferrous metal materials used in Simis sand casting include gray cast iron, ductile iron, alloy cast iron, carbon steel and low-alloy cast steel, which are suitable for equipment parts with high strength and wear resistance requirements. For non-ferrous metals, common materials include aluminum alloys, copper alloys (such as brass and bronze), magnesium alloys and zinc alloys, which are suitable for applications requiring lightweight, corrosion resistance.
1. Cast Iron
·Gray (Grey) Iron
·Ductile Iron
·Alloy Cast Iron: High chromium alloy cast iron, High nickel alloy cast iron, Silicon alloy cast iron, Aluminum alloy cast iron...
2. Cast Steel
·Carbon Steel: Low Carbon Steel, Medium Carbon Steel, High Carbon Steel,
·Alloy Steel: Low Alloy Steel,
3. Aluminum Alloy
·Aluminum Silicon Alloy (A356)
·Aluminum Magnesium Alloy (5052)
·Aluminum Zinc Alloy (7075)
·…
4. Other Alloys
·Brass
·Bronze
·Nickel Alloys
·Titanium Alloys
·…
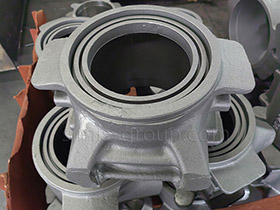
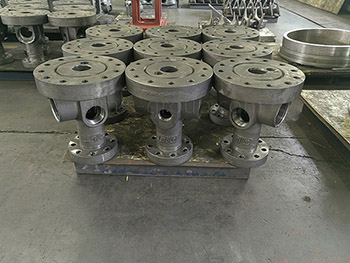
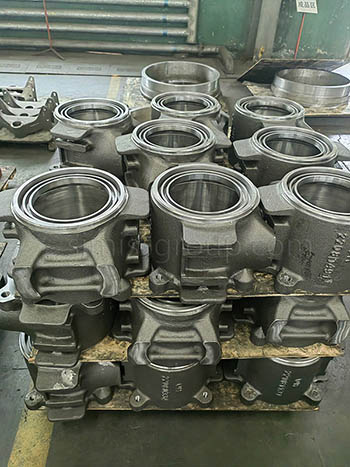
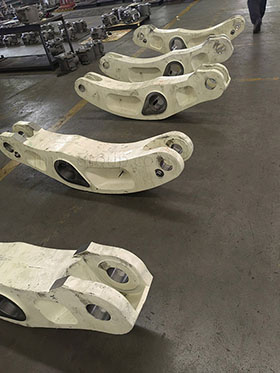