Simis Pressure Die Casting Foundry
Die Casting Factory Introduction
Simis Die Casting Foundry has an annual output of 6,000 tons, producing precision die-casting parts made of aluminum alloy, zinc alloy, copper alloy and other metal materials for the automotive, electronics, home appliances, aviation and other industries.
Simis Die Casting Foundry covers an area of about 9,000 square meters. There are several professional production workshops and fully automatic die-casting production lines in the plant, including smelting workshop, die-casting workshop, post-processing workshop, quality inspection workshop, etc. From metal smelting, casting, cooling, demolding to post-processing, each workshop is equipped with efficient production equipment and technical facilities.
Pressure Die Casting Process
Die Casting process overview
The die-casting process is to quickly inject molten metal into a precision mold under high pressure to cool and solidify it, so that the die-casting parts have clear details and stable precision. It is suitable for mass production of aluminum alloy, zinc alloy and other parts with complex shapes, precise dimensions and smooth surfaces.
1. Die-casting mold design
Die-casting molds are designed according to the product's size, structure, precision requirements and material properties to ensure the quality and production efficiency of castings.
2. Mold manufacturing
Die-casting molds are made of high-strength steel (such as H13, P20, etc.). Through precision machining, heat treatment and surface polishing, the durability, precision and surface quality of the mold are guaranteed.
3. Metal smelting and alloy preparation
Smelting: Select a metal material smelting furnace to heat to the melting temperature of the alloy so that the metal is completely melted into a liquid state.
Alloy preparation: According to the required alloy formula, necessary alloy elements are added to the molten metal to ensure that the metal composition meets the design requirements.
4. Die casting
The molten metal is injected into the preheated die-casting mold cavity through the die-casting machine injection system. Under extremely high pressure, the metal is quickly injected into the mold, so that the molten metal fills every detail of the mold, ensuring that the details of the casting are clear and there are no holes.
5. Cooling and solidification
The metal injected into the mold is rapidly cooled and solidified with the help of the mold cooling system to form the final shape, which depends on the size and complexity of the die casting.
6. Demolding and cleaning
After the metal cools and solidifies, open the mold and remove the casting from the mold.
After the die casting is demolded, there will be some burrs, overflows and residual metal, which can be cleaned by vibration cleaning machine, air sand cleaning, cutting, deburring and other methods to improve the surface quality and dimensional accuracy of the die casting.
7. Post-processing
Surface treatment: polishing, spraying, sandblasting, anodizing and other casting surface treatments to improve the beauty, corrosion resistance and wear resistance of the casting.
Heat treatment: high-strength aluminum alloy or other alloy castings may require heat treatment (such as aging treatment, annealing treatment, etc.) to improve the mechanical properties and hardness of the die casting.
8. Quality inspection
The die casting is comprehensively measured by quality inspection methods such as surface quality inspection, dimensional inspection, and mechanical property test to ensure that the die casting meets the requirements of the design drawings.
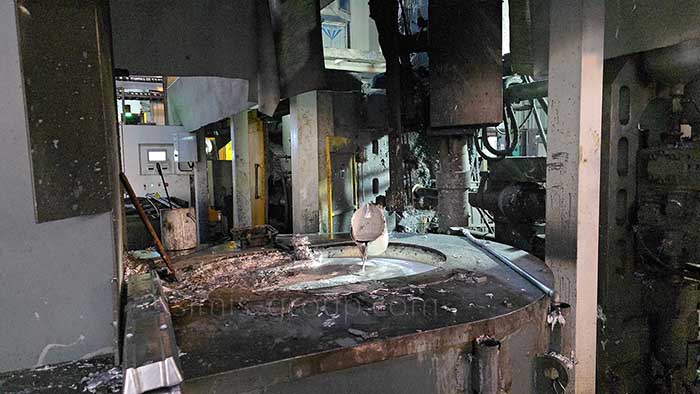
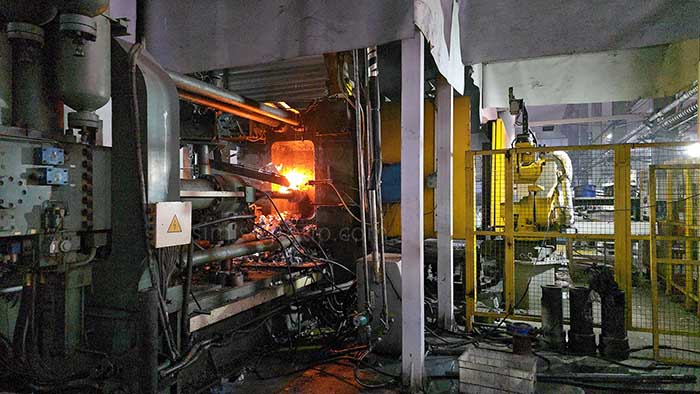
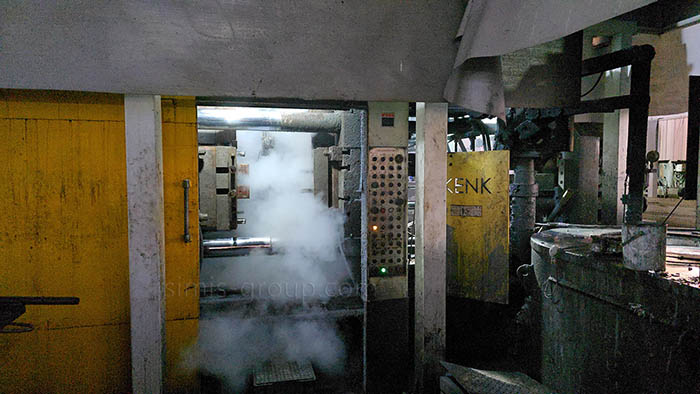
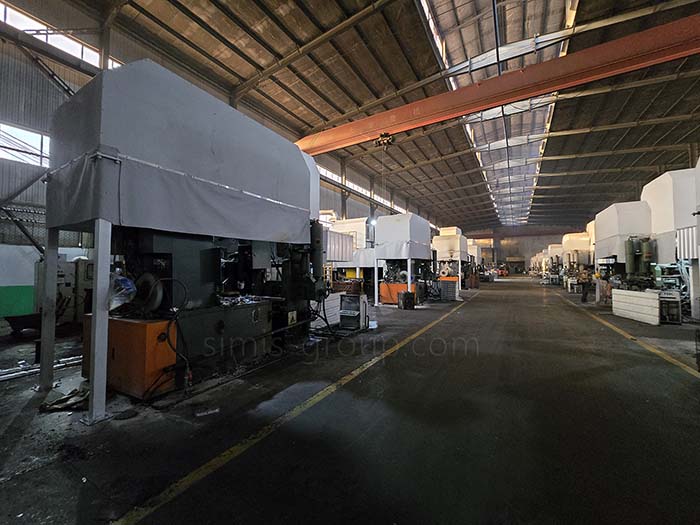
Materials For Pressure Die Casting
What metal parts can be cast in Simis die casting factory?
The metal materials mainly used for die casting in Simis Die Casting foundry are aluminum alloy, zinc alloy, magnesium alloy and copper alloy. Aluminum alloy is widely used in automobile, electronics and aviation industries due to its light weight, good mechanical properties and corrosion resistance; zinc alloy has high fluidity and low melting point, suitable for small and complex precision parts; magnesium alloy is often used in applications that need to reduce weight, such as automobile and aerospace due to its extremely light weight; copper alloy is used in some special needs due to its excellent wear resistance and corrosion resistance.
1. Aluminum Alloys:
·Aluminum-Silicon Alloys
·Aluminum-Magnesium Alloys
·Aluminum-Zinc Alloys
·Aluminum-Copper Alloys
·Aluminum-Manganese Alloys
·Aluminum-Titanium Alloys
·…
2. Other Alloys:
·Brass
·Bronze
·Nickel alloys
·Titanium alloys
·Copper alloy
·Magnesium alloy
·Zinc alloy
·…
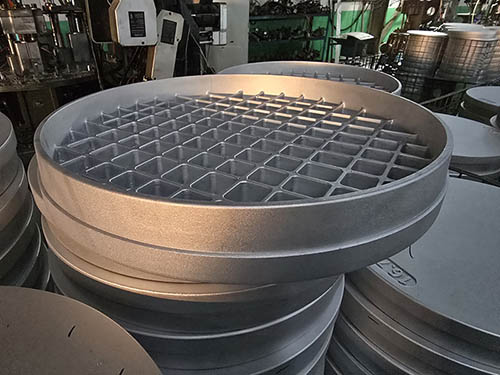
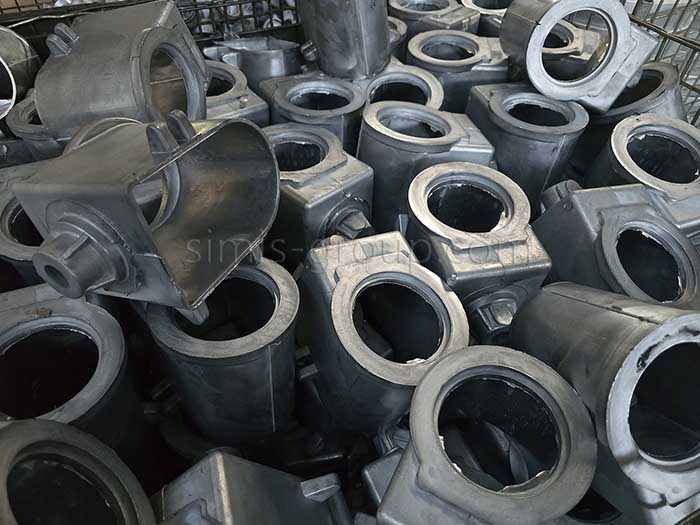
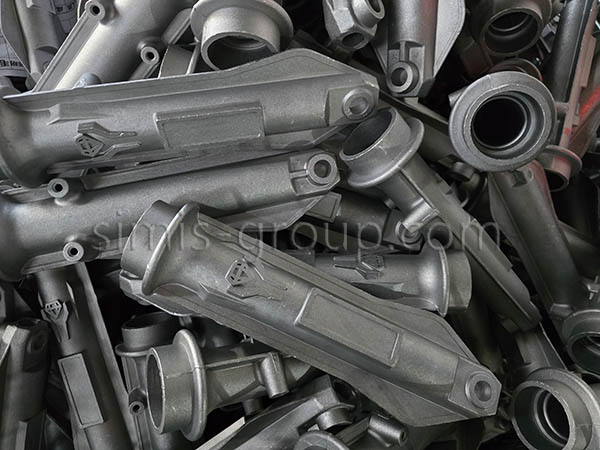
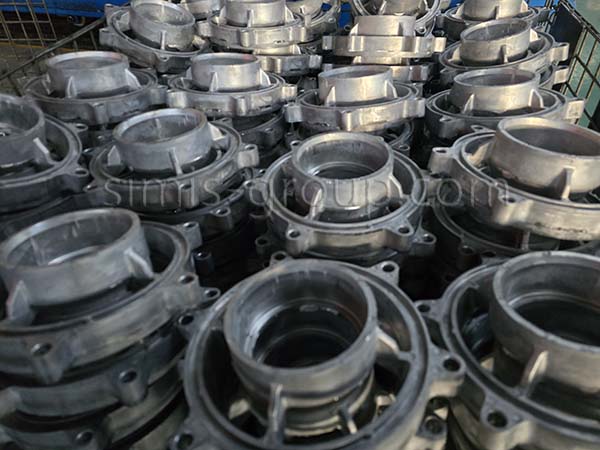