Simis Heat Treatment Workshop
Heat treatment workshop Introduction
The simis heat treatment workshop exists in every simis group casting and forging plant. The core functions of the workshop include heat treatment processes such as annealing, quenching, tempering, and normalizing of metal workpieces. The metal castings and forgings are heated, insulated, and cooled by controlling temperature, time, atmosphere, and other conditions to change their internal structure and mechanical properties. Heat treatment processes are widely used in the casting and forging of various metal materials such as steel, aluminum alloy, and copper alloy to improve the hardness, strength, toughness, and wear resistance of castings and forgings.
The SIMIS heat treatment workshop is equipped with advanced automation equipment, adopts a high-precision temperature control system and an intelligent production line, and realizes full-process automation control and data acquisition. The heat treatment workshop has a variety of heating equipment, such as induction heating furnaces, atmosphere furnaces, box furnaces, pit furnaces, etc., which can meet the processing needs of different castings and forgings. At the same time, the workshop is also equipped with cooling equipment, such as water cooling, oil cooling, air cooling, etc., which are used to quickly cool castings and forgings to achieve the required metal structure.
Heat Treatment Process
Heat Treatment process overview
The heat treatment process is a technical process that controls the internal structure and mechanical properties of metal materials by heating, heat preservation and cooling. According to different process requirements, common heat treatment methods include annealing, quenching, tempering, normalizing, carburizing, etc., the purpose is to improve the hardness, strength, toughness, wear resistance and other properties of the metal to meet the needs of specific use conditions. By precisely controlling the heating temperature, cooling rate and heat preservation time, heat treatment can adjust the microstructure of the metal, optimize the mechanical properties of castings and forgings, and improve the overall performance and service life of the parts material.
The choice of heat treatment method depends on the material, size, purpose and required performance of the castings and forgings. By reasonably selecting different heat treatment processes, the hardness, strength, wear resistance, plasticity and other properties of the metal can be improved in a targeted manner, thereby meeting the requirements of various mechanical parts in actual use.
1. Annealing
Annealing is the process of slowly cooling a metal after heating it to a certain temperature and keeping it for a certain period of time.
Annealing methods can be divided into ordinary annealing, spheroidizing annealing, stress relief annealing, etc. according to different cooling methods.
2. Quenching
Quenching is to heat the metal to a certain temperature, usually above its critical point, and then cool it quickly (usually with water, oil or air). This process can significantly increase the hardness of the metal surface.
The quenched metal usually becomes brittle due to excessive internal stress, so tempering is required to release the internal stress and reduce brittleness.
3. Tempering
Tempering is the process of reheating the quenched metal to a certain temperature, keeping it for a period of time, and then slowly cooling it.
The temperature and time of tempering will directly affect the properties of the metal, and it is usually divided into low-temperature tempering, medium-temperature tempering and high-temperature tempering.
4. Normalizing
Normalizing is to heat the metal to a temperature higher than the annealing temperature but lower than its melting point, and then cool it in the air.
Compared with annealing, normalizing has a faster cooling rate and can obtain a more uniform structure.
5. Carburizing
Carburizing is heating low carbon steel to high temperature (usually 900-950°C) and treating it in a carbon-containing atmosphere, so that carbon atoms penetrate into the metal surface, thereby increasing the surface hardness and wear resistance. Carburizing is usually used for high-load parts such as gears and bearings.
6. Nitriding
Nitriding is heating steel parts to medium-low temperature (usually 500-550°C) and placing them in a nitrogen-containing atmosphere (such as ammonia) to allow nitrogen atoms to penetrate into the metal surface.
Nitriding is similar to carburizing, but nitriding is carried out at a lower temperature, does not require subsequent quenching treatment, and can obtain a more uniform and dense surface hardened layer.
7. Induction Hardening
Induction hardening is to heat the metal surface through the magnetic field generated by high-frequency current, quickly heat it to the quenching temperature, and then cool it with water or oil to achieve hardening.
Induction hardening is often used for mechanical parts, such as gears, bearings, etc., which require high surface hardness and good internal toughness.
8. Surface Hardening
Surface hardening is to locally heat the metal surface through different heating methods (such as laser, flame, etc.), and then quickly cool it to achieve the effect of surface hardening.
9. Martempering
Martempering is a process in which the workpiece is heated to a relatively high temperature, then quickly cooled to a relatively low temperature and maintained for a certain period of time during the quenching process, and finally cooled to room temperature.
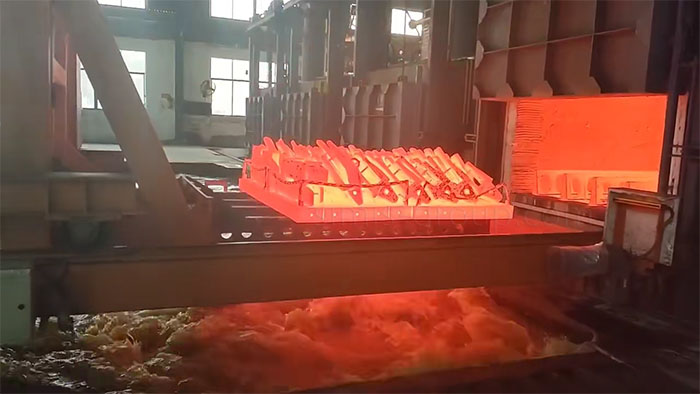
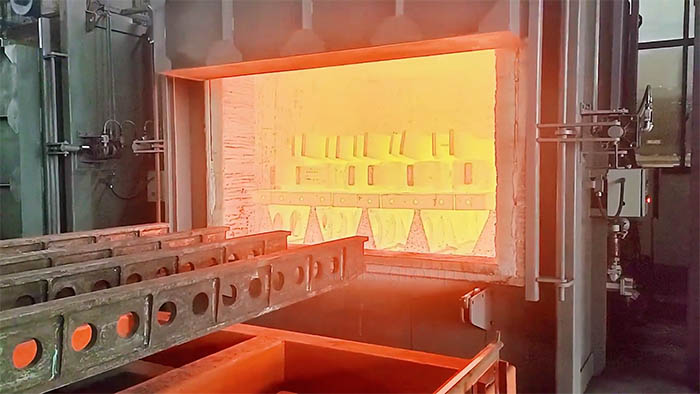
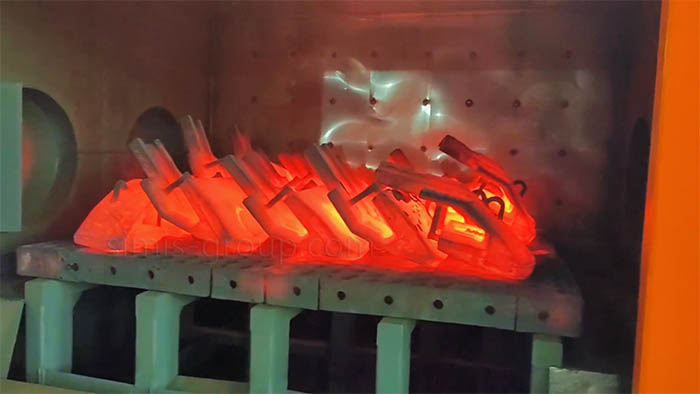
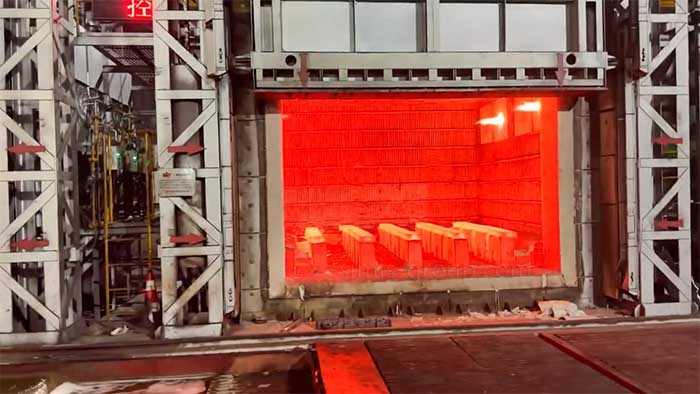
Materials For Heat Treatment
What metal parts can heat treatment?
Heat treatment can be applied to a variety of metal materials, mainly including carbon steel, alloy steel, stainless steel, tool steel, aluminum alloy, copper alloy and titanium alloy. Different metal materials can optimize their performance to meet specific application requirements through different heat treatment methods. Carbon steel and alloy steel are often used to improve hardness and strength through annealing, quenching, tempering and other processes; stainless steel is often used to improve corrosion resistance and mechanical properties; tool steel is used to manufacture high-hardness, high-wear-resistant tools and molds; aluminum alloys are mainly improved through heat treatment to improve strength and toughness; copper alloys are enhanced through annealing and solution treatment to enhance their conductivity and corrosion resistance; titanium alloys are used in aviation, aerospace and other fields to improve their strength and high temperature resistance through heat treatment.
1. Steel
·Carbon Steel: Mild Steel, Medium Carbon Steel, High Carbon Steel,
·Alloy Steel: Low alloy steel, High alloy steel,
·Stainless steel: Austenitic stainless steel, Ferritic stainless steel, Martensitic stainless steel, Duplex stainless steel, ...
·Tool Steel: High speed tool steel, Cold work tool steel, Hot work tool steel, ...
2. Aluminum Alloys
·Aluminum-Silicon Alloys
·Aluminum-Magnesium Alloys
·Aluminum-Zinc Alloys
·…
3. Other Metal Alloys
·Brass
·Bronze
·Nickel alloys
·Titanium alloys
·…
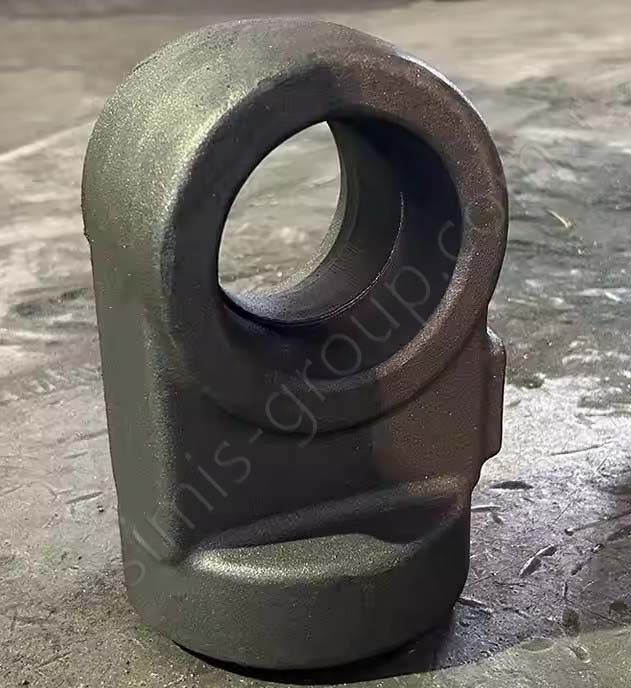
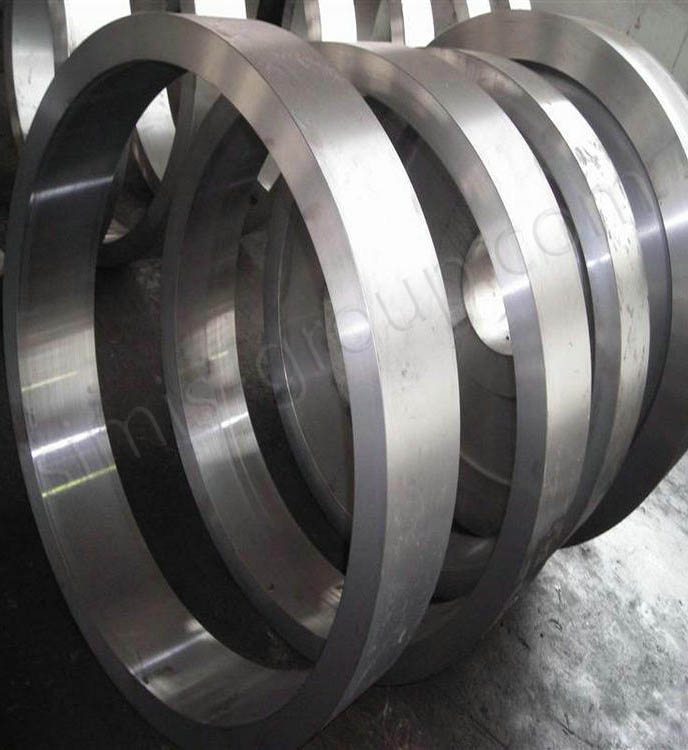
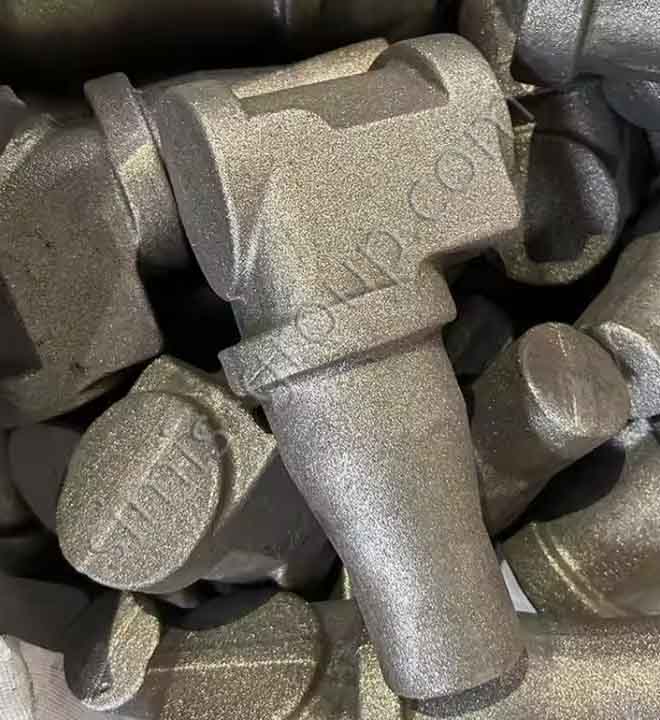
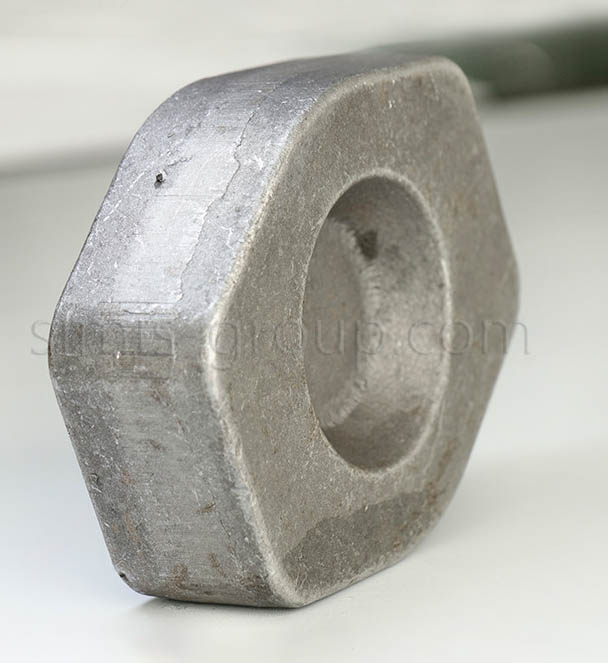