Simis Shell Mold Casting Foundry
Shell Mold Casting Factory Introduction
Simis Shell Mold Foundry has an annual output of about 5,000 to 7,000 tons, mainly producing high-precision, high-surface quality, small and medium-sized complex castings. Customizable metal materials include gray cast iron, ductile iron, alloy cast iron, carbon steel, alloy steel, aluminum alloy, etc., which are used in automobile manufacturing, valve accessories, engineering machinery, pump accessories, general machinery and other industries.
Simis Shell Mold Foundry covers an area of about 9,000 square meters and has a complete range of shell mold casting production equipment and automation systems, such as shell mold making machines, automatic pouring systems, melting equipment, sand core production systems, shot blasting machines and other automation equipment. Multiple shell mold casting production lines use intelligent control systems, and automatic mold coating, cooling, demolding and other links are automated; it is also equipped with manual pouring workshops to meet the production of orders of different quantities and customers' needs for high-precision castings.
Shell Mold Casting Process
Shell Mold Casting process overview
Shell mold casting is a high-precision casting process that forms a hard thin shell mold by coating a layer of coated sand mixture on a metal mold and heating and curing it, and then pouring liquid metal to produce complex, high-precision, small and medium-sized castings. This process is characterized by high mold dimensional accuracy, excellent surface quality and strong consistency. It is suitable for mass production of parts with complex shapes and high requirements, such as valve bodies, pump housings, mechanical parts, etc., and is widely used in the fields of automobiles, machinery and engineering equipment.
1. Mold design and manufacturing
According to the casting design requirements, make a metal mold (usually cast iron or steel mold) for shell casting cavity production.
2. Coated sand preparation
Coated sand is a mixed material composed of quartz sand coated with a layer of thermoplastic or thermosetting resin, which has good fluidity and molding properties.
3. Heating the metal mold
The mold is preheated to a specified temperature (usually 250-350℃) and heated evenly to ensure the curing effect of the sand shell.
4. Filling and curing of coated sand
The coated sand is injected into the heated metal mold, and the coated sand is evenly filled into the mold cavity through vibration or gravity.
The coated sand quickly softens and solidifies to form a hard shell of a certain thickness after contact with the heated mold.
The mold is flipped or dumped to remove excess uncured coated sand to ensure uniform thickness of the sand shell.
5. Shell demolding
After curing, open the mold parting surface and carefully remove the formed sand shell mold.
6. Shell assembly and bonding
The finished upper and lower mold sand shells are bonded by adhesive or heating to ensure that the mold is tightly closed and leak-free. If a sand core is required, a prefabricated sand core can be placed in the mold cavity before assembly.
7. Mold preparation and pouring
The mold is placed on a pouring platform or sand box and fixed to prevent movement during pouring.
Molten metal (such as steel, iron or aluminum) is injected according to the designed pouring channel.
8. Cooling and demolding
After the molten metal is cooled, the sand shell mold is opened for demolding and the casting is taken out.
The shell mold will become brittle during the cooling process and is easy to break and remove.
9. Casting cleaning and post-processing
Remove the residual sand shell on the surface of the casting and clean the surface oxide scale by shot blasting or sand blasting.
Cut off the pouring system and riser, and grind, finish and check the size of the casting.
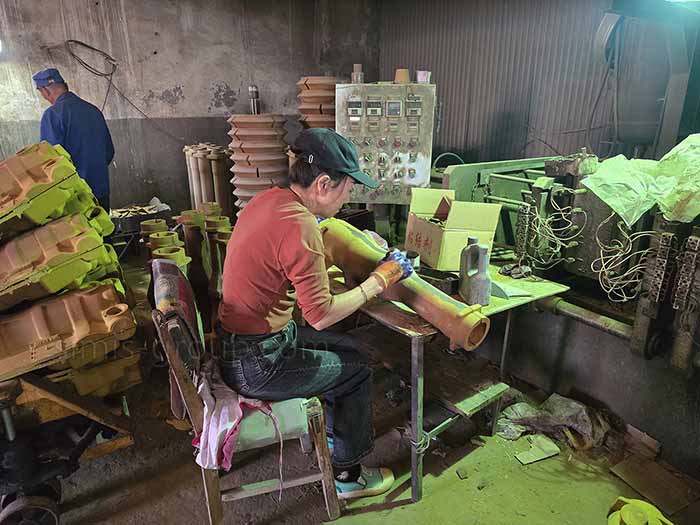
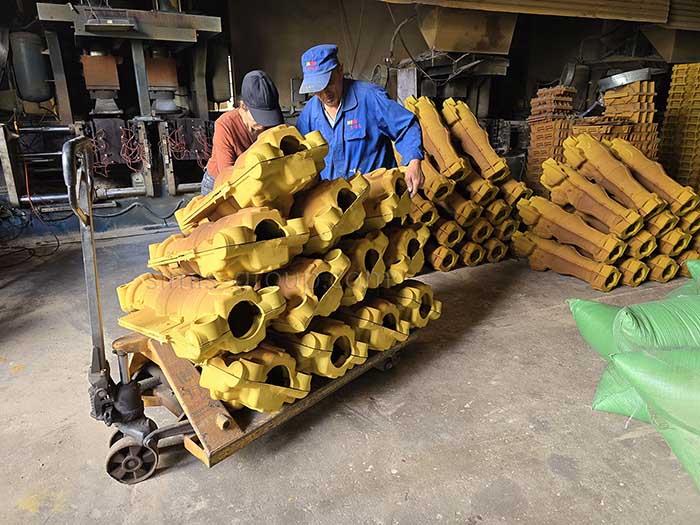
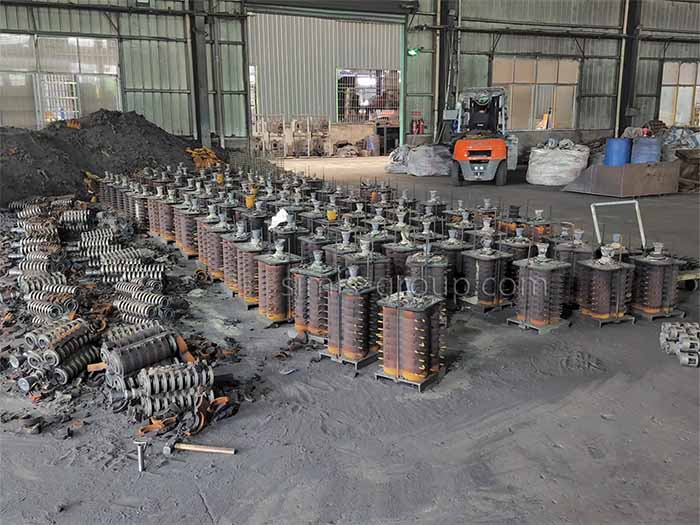
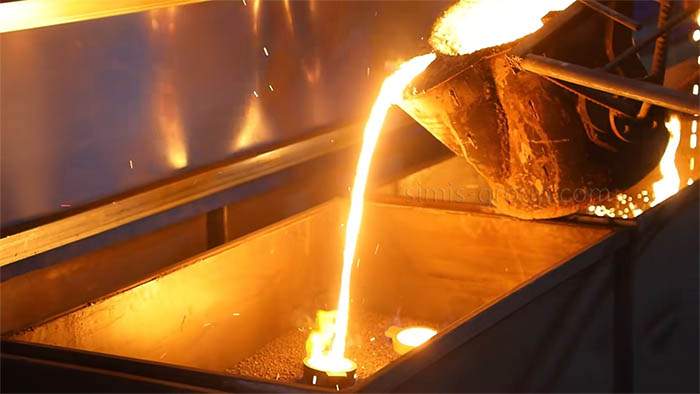
Materials For Shell Mold Casting
What metal parts can be cast in Simis Shell mold casting factory?
SIMIS Shell Mold Foundry is able to cast parts made of different metal materials. Commonly used materials for shell casting include gray cast iron, ductile iron, carbon steel, aluminum alloy, copper alloy, etc. We can customize parts for different industries based on different materials, including automotive engine parts (such as cylinder heads, intake and exhaust manifolds), hydraulic valve bodies, pump housings, motor housings, gearbox housings and other mechanical parts with complex shapes and high precision requirements.
1. Cast Iron
·Gray (Grey) Iron
·Ductile Iron
·Alloy Cast Iron:High Chromium Alloy Cast Iron, High Nickel Alloy Cast Iron, Silicon Alloy Cast Iron, …
2. Cast Steel
·Carbon Steel: Mild Steel, Medium Carbon Steel, High Carbon Steel,
·Alloy Steel: Low Alloy Steel, High Alloy Steel,
·Stainless steel: Austenitic Stainless Steel, Ferritic Stainless Steel, Martensitic Stainless Steel, Duplex Stainless Steel, ...
3. Aluminum Alloys
·Aluminum-Silicon Alloys
·Aluminum-Magnesium Alloys
·Aluminum-Zinc Alloys
·…
4. Other Alloys
·Brass
·Bronze
·Nickel alloys
·Titanium alloys
·…
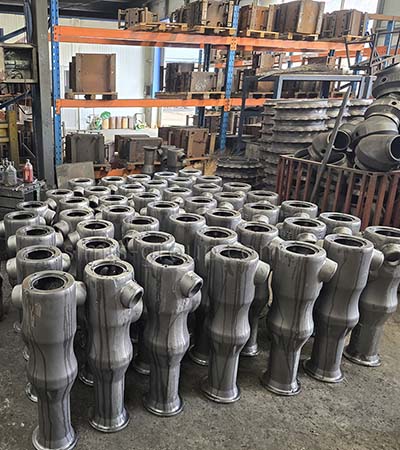
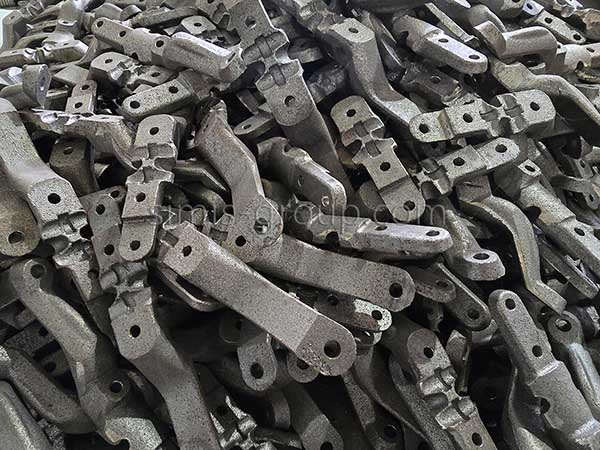
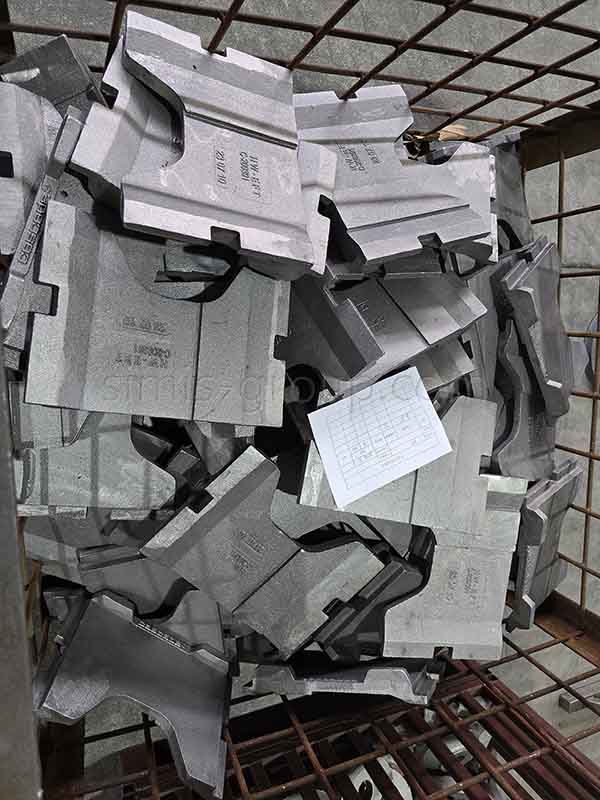
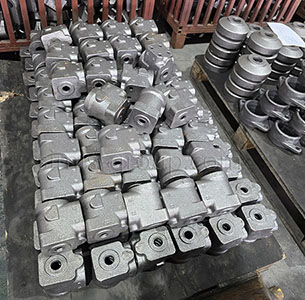